Contents
- Key Differences between Injection Molding and Compression Molding
- What is Injection Molding?
- What is Compression Molding?
- Differences between Injection Molding and Compression Molding
- Key Advantages and Disadvantages of Injection Molding
- Key Advantages and Disadvantages of Compression Molding
- When to Choose Injection Molding?
- Where to Find Custom Plastic Injection Molds?
- Conclusion
Key Differences between Injection Molding and Compression Molding
Injection molding is a highly scalable industrial process that enables manufacturing plants to produce millions of parts per annual, a key factor in the exponential growth of the medical device industry in the US.
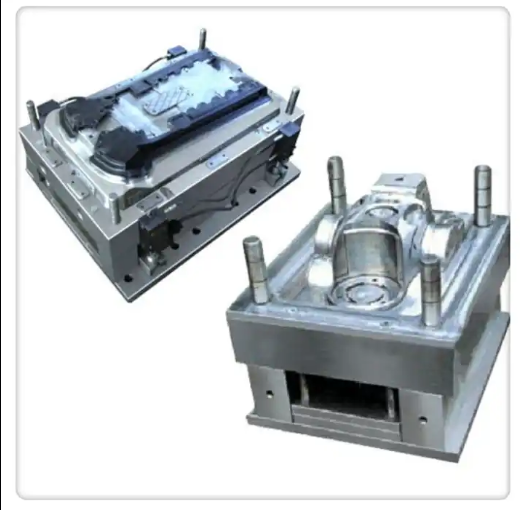
However, injection molding is far from the only manufacturing process in the market. Compression molding is another superb contender that also brings a whole different set of benefits. This article will highlight the key differences between injection molding and compression molding to help you, as business owners, get started.
What is Injection Molding?
The injection molding process involves pouring molten materials, which can be plastic, metals, or glass, into a pre-cast plastic or metal mold, allowing them to take on the shape of the mold itself. Once the materials have cooled down and hardened, the finished products will be taken out by the engineers and put through additional processing.
Injection molding is a popular manufacturing process, as demonstrated by the size of the global market. There is strong growth for this market in the years to come as well.

What is Compression Molding?
Compression molding is another manufacturing method that actually predates injection molding. This process involves a mold, a charge or multiple charges, and a compression machine. The process goes like this.
- It begins with the engineer loading the pre-heated charges, typically made of soft and malleable materials, into the mold.
- They then start the compression machine, which compresses the upper part of the mold and the lower part together, changing the shape of the charges.
- As the process goes on, the charges will gradually take on the shape of the mold itself.
- The finished products will then be taken out for further processing.
Differences between Injection Molding and Compression Molding
industrial processes that force materials into certain shapes using molds. Where they differ is in the “How”: In injection molding, engineers inject molten materials into the mold so that the end product takes on its shape. Meanwhile, in compression molding, the shape is achieved through compression force produced by the press.
The two processes also use different materials. Injection molding can be paired with a wide variety of materials, including thermoplastics, metals, and glass. On the other hand, however, compression molding can only take on thermoplastics due to their being malleable enough for the process.
Finally, as business owners, you will have to take into account the different sets of business advantages and disadvantages the two processes bring.
Key Advantages and Disadvantages of Injection Molding
Injection molding enables you to create complex products with the right molds, due to how molten materials easily seep into the tiny holes in the mold. For example, with the right electrical appliance mold, your business can easily create high-quality parts with ease. Even better, injection molding enables your business to scale relatively easily thanks to the ease of automation.
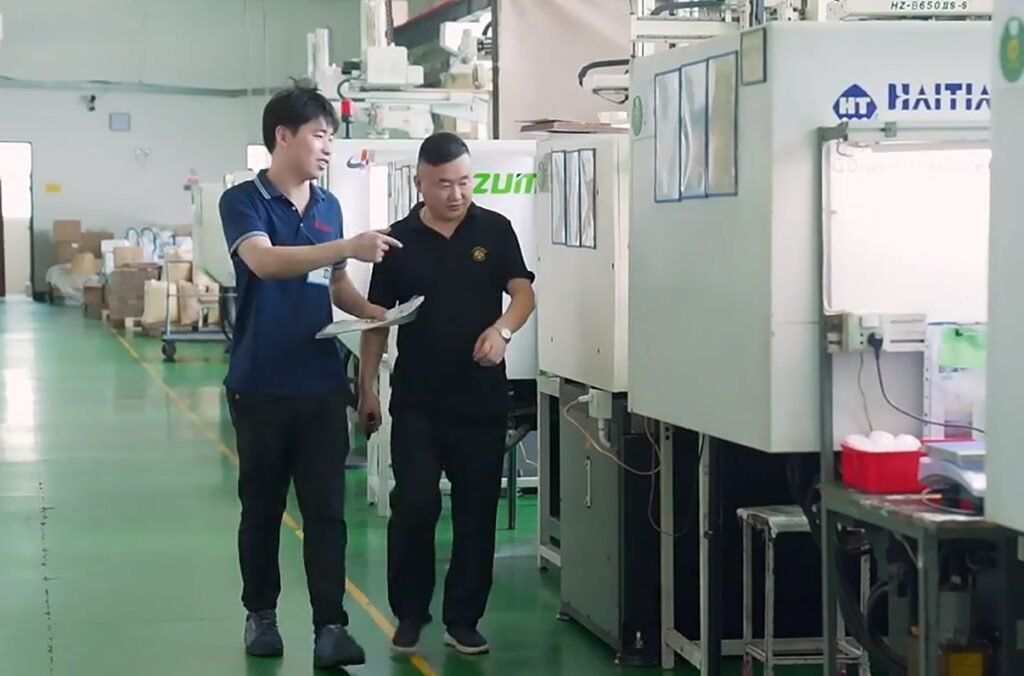
However, the initial setup costs for an injection molding business can be quite high. Mold design is an important factor to consider, because one simple mistake can easily cost you your entire assembly line. Furthermore, without high-quality injection molding tools, production might be affected in the long run.
Key Advantages and Disadvantages of Compression Molding
The initial setup costs for a compression molding manufacturer are much lower, on the other hand. As compression molding chiefly works with large and simple parts, mold design is not quite as intensive, so you will not have to spend a lot of initial costs on this aspect. Mold design for compression molding also offers more flexibility compared to injection molding, and this flexibility carries over to the production process as well.
That said, compression molding requires much more labor costs, as the production cycle is longer and there is a fair bit of manual labor involved. This means that it will be tough for businesses to scale a compression molding production line. There is also the fact that compression molding cannot be used to make complex parts with intricate designs and high precision.
When to Choose Injection Molding?
Injection molding is the premier choice if you wish to create a reliable production line that can handle complex molds and designs. Even though the initial costs can pose a challenge, which can be offset by finding the right injection molding company, the business benefits that injection molding offers in the long run far outweigh the costs. As demands for high-volume orders of complex medical parts or car parts increase, your business can confidently handle them with ease thanks to injection molding.
Where to Find Custom Plastic Injection Molds?
The first step for every manufacturer to take before they can set up their injection molding production line is to find the right injection molds. Plastic injection molds are a good place to start, because they do not cost quite as much as their metal counterparts. Furthermore, with the help of experts in the field, you can customize the plastic molds to fit your preferences or the requirements of your clients.
With over 23 years in the industry, KuiXing can confidently accommodate all your needs when it comes to custom plastic injection molds. We are experts when it comes to mold design, and we have worked with international partners such as BMW, Audi, Foxconn, and Samsung.
Conclusion
The key differences between injection molding and compression molding lie in how they work. Injection molding involves injecting molten materials into a mold so that they take on the shape of said mold. Meanwhile, compression molding manufactures products by compressing a pre-heated charge inside a mold until it achieves the shape of the mold itself.
Both injection molding and compression molding are popular manufacturing processes with their own benefits and downsides. For businesses that are looking for a solution that scales with ease, injection molding is the superior choice since it enables high-precision production and automation capabilities, in spite of the high initial costs and complex mold design process.
References:
- https://www.precedenceresearch.com/plastic-injection-molding-market#:~:text=The%20global%20plastic%20injection%20molding,4.8%25%20from%202021%20to%202030.https://www.precedenceresearch.com/plastic-injection-molding-market
- https://www.statista.com/outlook/hmo/medical-technology/medical-devices/united-states