Ever wonder how a syringe is made? With its specific shape and different sizes, a syringe is almost impossible to make by hand, so a standardized industrial process is needed to produce them en-masse with laser-focus precision. Injection molding is what this process is called, and it is the key to the success of our industrialized world. In fact, the injection molding market size is expected to grow steadily at a rate of 4.8% from 2022 to 2030, demonstrating how important it is to the global market as a whole.
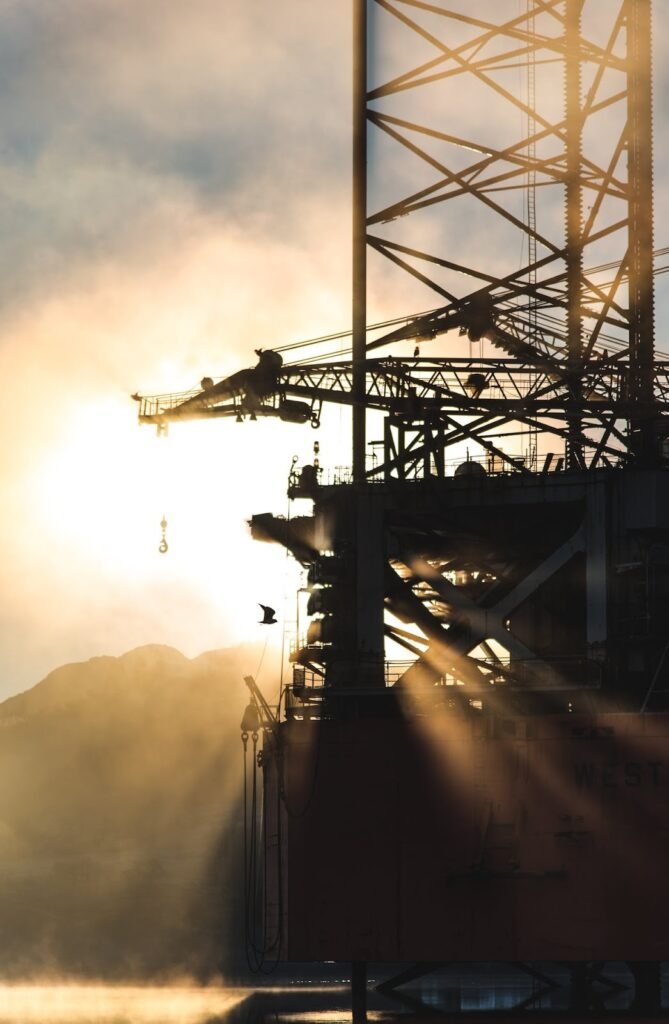
However, because injection molding is such a highly standardized process with little publicity, how it works is generally not known to the public. Understanding the injection molding process, as well as its strict requirements and specifications, will allow you to not only appreciate the craft but also find the best injection molding companies around more easily, thereby cutting manufacturing costs.
What is Injection Molding?
Injection molding is, first and foremost, an industrial process to manufacture products or devices with very specific shapes and specifications. Because the process can be done very quickly and semi-automated, it enables manufacturing plants to produce thousands of products continuously. This means that it requires, at the very least, advanced tools and workers with expertise in the field.
In the injection molding process, molten materials are injected into a mold that shares the same shape and size as the finished product. The material will then slowly cool down and harden, taking up the shape of the mold itself. Coolants such as water or oil will be used to speed up the cooling process considerably. Once the material has been properly cooled and hardened, injection molding specialists will take off the mold, and the product will be ready for the next steps.
During this process, there are several points to keep in mind:
- Mixing materials: The material used in this process is often a mix of several different materials to give the finished product special properties or colors.
- Mold materials: The molds used for the injection molding process will have to be reused intensively, so it is important that they should be made from high-quality materials that will not degrade easily. Steel molds are the industry standard for injection molding, but they can be quite expensive. Aluminum molds are also quite popular.
- Mold design: When designing molds, engineers have to be particularly careful with the specifications, as one slight error means mass defects for the entire production line. Sometimes, a mold may have several cavities to create geometric designs.
The Different Materials for Injection Molding
Depending on the product’s specifications, engineers will use many different materials for injection molding. The most popular choices are plastic injection molding, glass injection molding, and metal injection molding.
Plastic Injection Molding
Thermoplastic materials such as acrylic, Acrylonitrile Butadiene Styrene (ABS), and nylon, are the premier choices for the injection molding process. These materials are generally very malleable with a vast range of resistance properties, offering plenty of options for manufacturing plants. The downside of plastic injection molding is that the materials tend not to do so well against water damage, except for acrylic.
Metal Injection Molding (Die-Casting)
Metals-based products are indispensable for daily life, and metal injection molding is a useful way to produce them en-masse with consistent results. As with the plastic injection molding process, molten metal materials are injected into a mold to take on its shape before going on a cooling process. The most commonly used metals are zinc, copper, aluminum, and lead, which tend to be malleable.
Glass Injection Molding
Glass is an extremely malleable material that has been used for centuries, so naturally, it is also a great choice for the injection molding process. Glass injection molding has seen breakthroughs in recent years, which makes the process even more cost-effective and energy-efficient.
Injection Molding in Different Industries
As one of the most important industrial processes, injection molding finds plenty of uses in different industries, from FMCG to complex manufacturing industries such as airplane parts and medical devices.
Medical Injection Molding
As the example with the syringe shows, medical devices require extreme precision and zero defects, something that traditional artisans cannot deliver consistently. Medical injection molding enables businesses to produce these devices with extreme precision en masse, preventing losses of life and medical accidents.
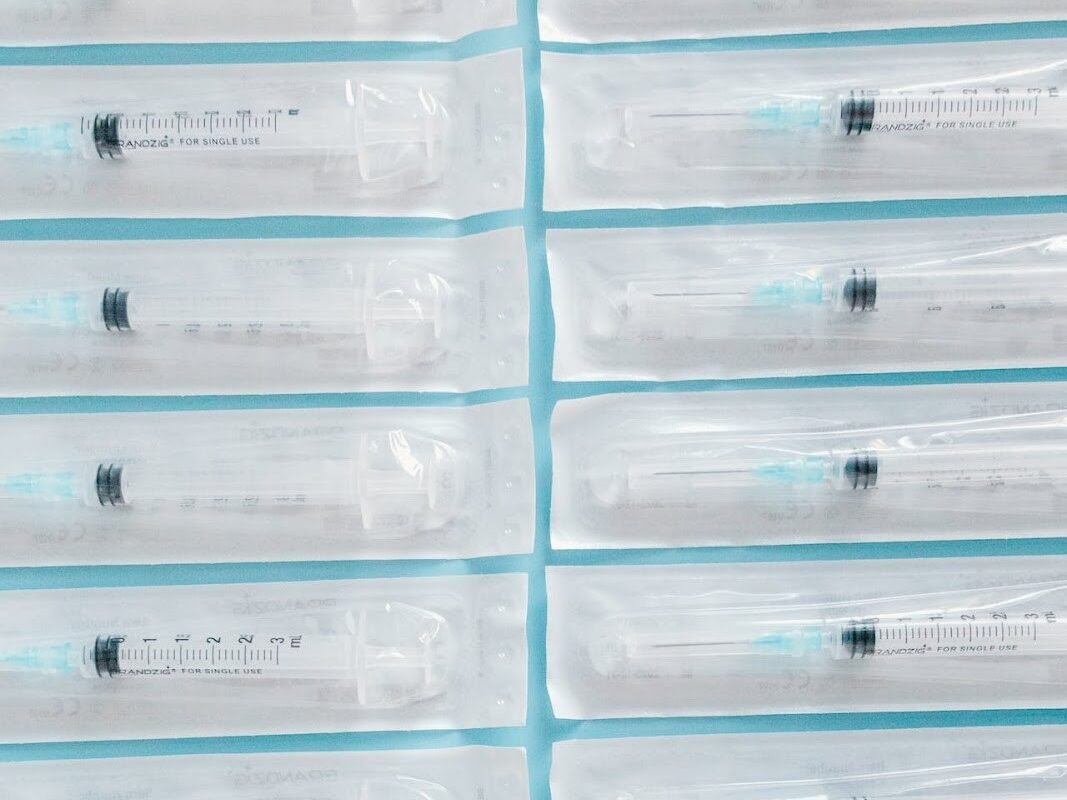
Auto Parts Injection Molding
Injection molding is used extensively in car manufacturing plants across the world. Car parts have to be produced in compliance with strict specifications guidelines, as a single defect means that parts might not fit with one another. Auto parts injection molding offers manufacturing plants not just high precision but also scalability, enabling them to meet high demands with ease.
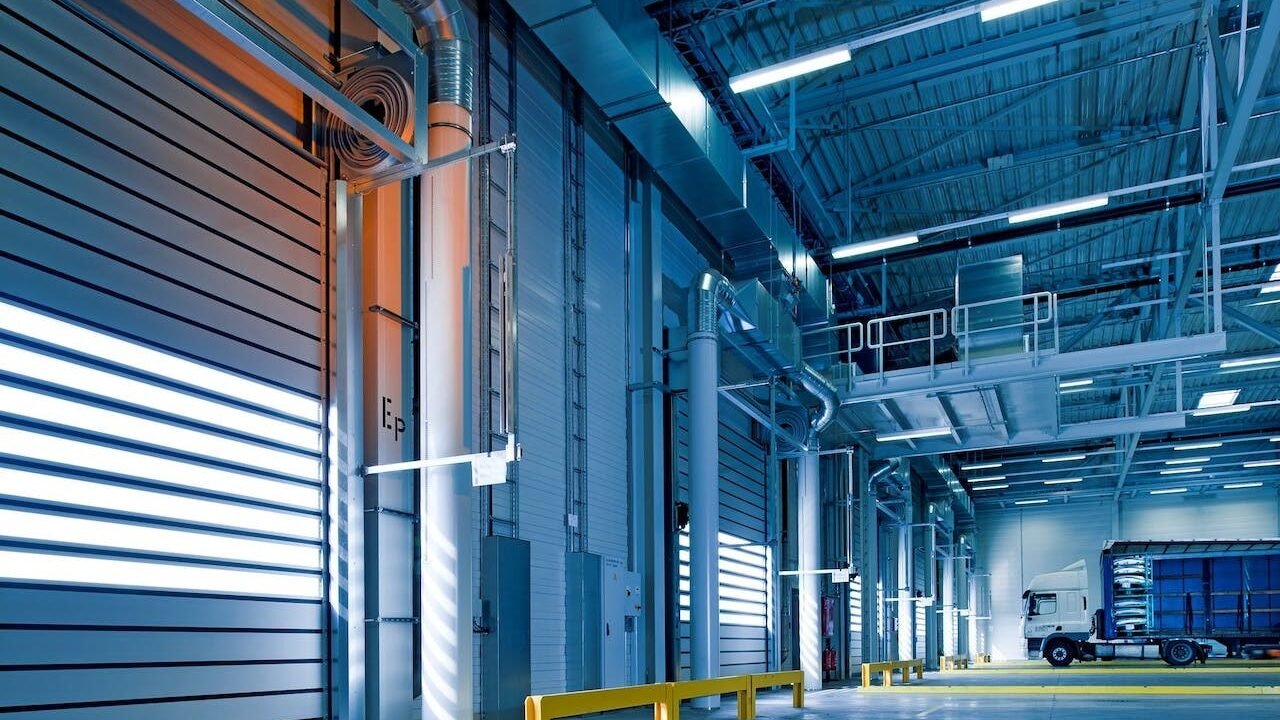
Food & Beverage Injection Molding
Though products in the F&B industries generally don’t require much precision, they are in extremely high demand. Businesses wishing to meet this quota will find injection molding a godsend, as this process is highly scalable and cost-effective. It is also highly automated, so there is no high demand for human labor.
Finding the Best Injection Molding Companies
Injection molding is a complex process that requires high precision and technical know-how, so businesses looking for injection molding partners should pay extra attention. Just one single defect can cause major business risk.
Here are some top qualities you should keep an eye out for when finding the best injection molding companies:
- Design expertise: Designing reliable and robust molds takes years of experience and expertise, but this step is essential in manufacturing reliable products. Companies with extensive experience in molding are naturally your best partners.
- Scalability: Injection molding is a scalable process, but the injection molding company itself must have prior experience and the facilities for scaling to go smoothly.
Conclusion
mold that define the shapes and sizes of the finished products. The molten materials then go through a cooling and hardening process with the help of coolants, and once they are hardened, engineers will open up the mold to take out the finished products.
As injection molding is a scalable process that produces highly precise products, it is often used in a wide range of industries, including medical devices, auto parts, and computer parts. For more information on injection molding, don’t hesitate to contact our injection molding experts.
References:
https://www.grandviewresearch.com/industry-analysis/injection-molding-market-report
https://www.techbriefs.com/component/content/article/39971-glass-injection-molding
2 Responses