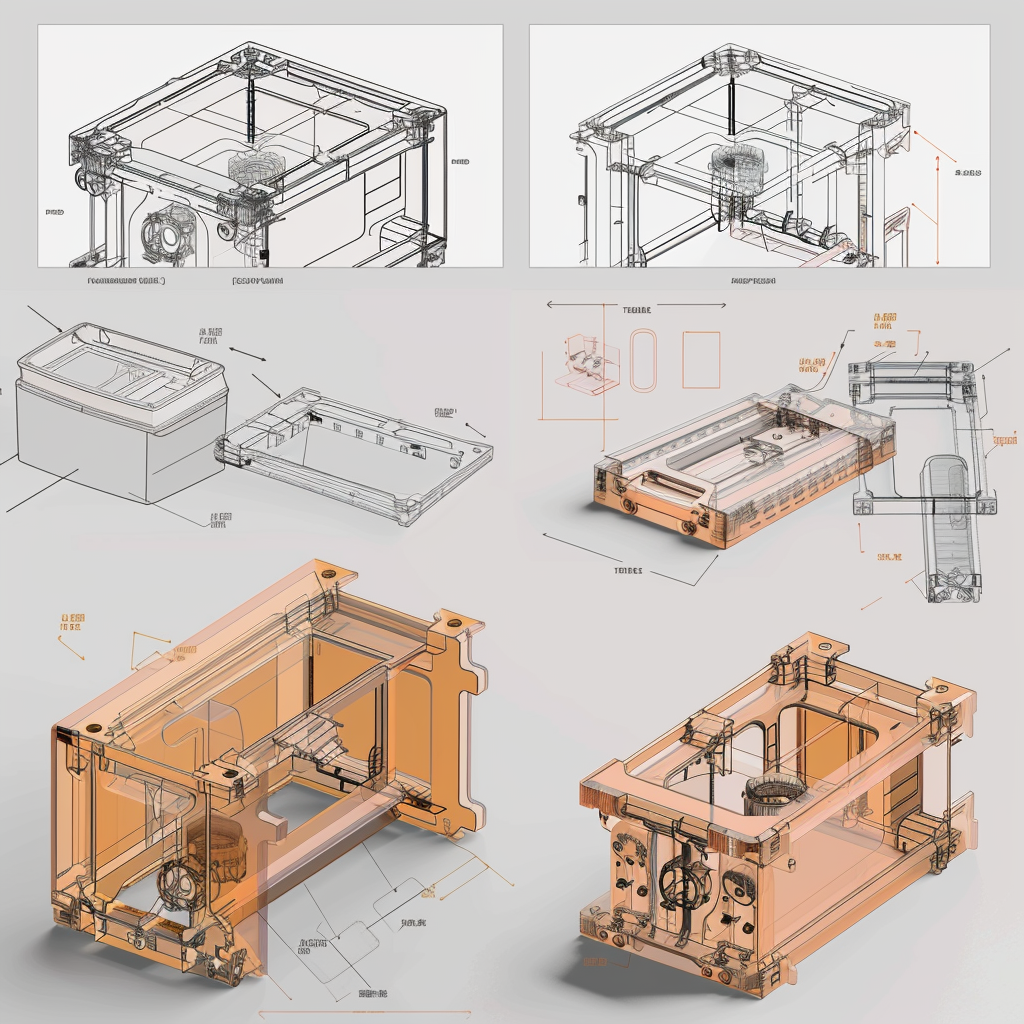
1. Customer requirements
(1) Product batch size: Understanding the product batch size has a great impact on determining the size of the mold, the number of cavities, steel materials, positioning systems, cooling system design, etc.
(2) Countries or regions where molds are sold: Each country or region has different safety standards for molds, and there are differences in the standard parts used, the position of the injection machine push rod hole, and the size of the positioning ring.
(3) Whether the mold needs to be produced automatically: The mold is installed on the injection molding machine, and the size of the mold must match the injection molding machine. To realize automated production, first of all, the push-out distance of the mold must be sufficient, and push-out and reset must be safe and reliable.
(4) Main parameters of the injection molding machine model: modulus; nozzle parameters (nozzle spherical surface SR, nozzle aperture, nozzle outer diameter, positioning aperture, nozzle maximum extension length, etc.); mold installation parameters (code die hole, code die Groove size); mold opening stroke and maximum distance between moving and fixed platens; push-out mechanism; maximum injection volume; maximum clamping force, etc.
(5) Packaging requirements.
(6) Mold delivery location and transportation method.
2. Plastic parts requirements
(1) Understand the assembly drawings and parts drawings of plastic parts. Includes three-dimensional views (3D) and plan views (2D). To understand the structure and function of plastic parts.
(2) Dimensional accuracy requirements for plastic parts. Including appearance and assembly dimensions.
(3) Color and material of plastic parts. Including whether the plastic parts are transparent, shrinkage rate, and whether the plastic is corrosive.
(4) Requirements on the surface of plastic parts. Including whether it is polished, etched, sparkled, sandblasted, and the size of the demoulding angle (whether it must be straight).
(5) Understand the assembly position of plastic parts. When setting up push rods, gates, inserts, etc., try not to affect the appearance.
(6) Whether the wall thickness of plastic parts is too large. If it can be improved to average material thickness, the production and cost of plastic parts can be reduced. However, it needs to be approved by the customer.
(7) When the dimensional accuracy of plastic parts is too high, careful consideration should be given. Avoid dimensional accuracy that cannot be guaranteed during injection.
(8) Pay attention to whether the plastic parts have inserts. If there are inserts, installation, positioning, anti-rotation and preheating must be considered.
(9) Whether the plastic parts are processed after molding, including electroplating, secondary injection, etc.
3. Mold requirements
(1) Notice of mold opening. Understand the number, name, plastic, mold number and other matters of the plastic part from the mold opening notice.
(2) Mold life and molding cycle.
(3) Whether the mold material is heat treated and the selection of standard room.
(4) The operation mode is automatic, semi-automatic, or manual.
(5) The mold base is a two-plate mold, an I-shaped mold or a straight mold.
(6) Gate form and location.
(7) Determination of parting surface.
(8) Launch location and form.
(9) Side core pulling mechanism and core pulling power (such as mold opening force, hydraulic press or spring force, etc.).
(10) Whether there is a heating device when designing the temperature control system.