Precision is always a key factor in all industries, as parts and devices have to follow strict specification guidelines so that they can work together. However, throughout the history of industries, absolute precision has been quite elusive, and manufacturers often struggle to consistently create parts that share the same sizes and dimensions.
That was the case until injection molding came about. Injection molding is an innovative production method that helps manufacturers easily produce parts and other products at scale with high precision, ensuring consistent quality and functionality.
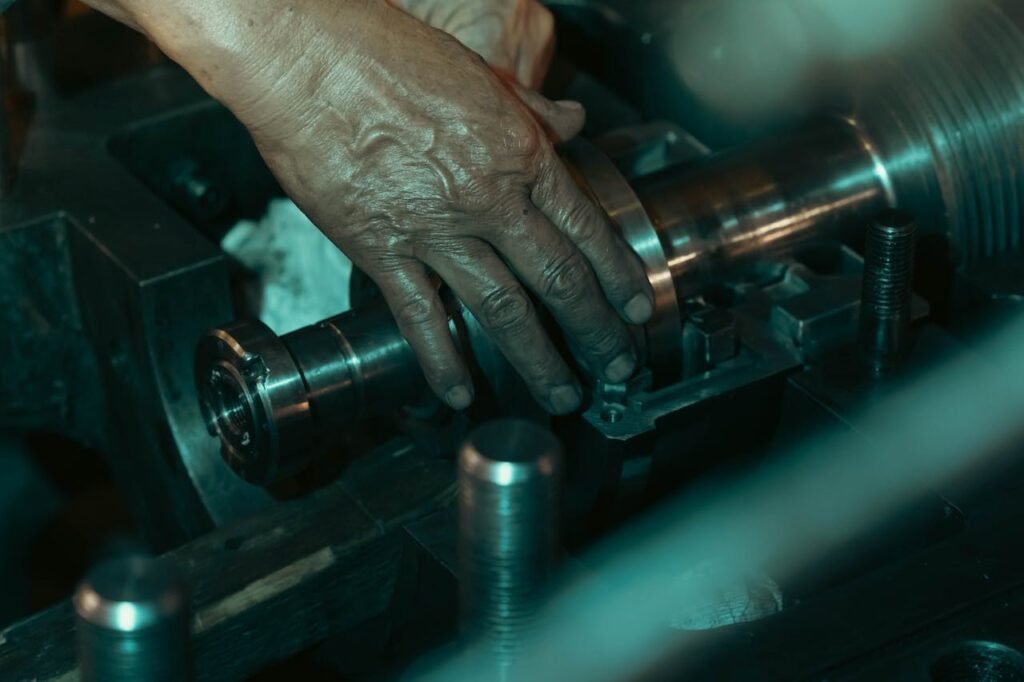
The World before Injection Molding
Manufacturing has been around since as early as the Neolithic era of human history. Stone tools were found as early as 7,000 BC, when civilizations had not yet flourished. In the years afterwards, better tools were gradually developed, made from bronze and then iron. However, even though these tools were capable of high production capabilities, the manners of production largely remained the same until the Renaissance Era, when guilds and independent artisans gradually took control of manufacturing.
The Industrial Revolution was one of the most important turning points in human history, as it changed how humans produced new tools and products. Mass production has become the norm, and new production methods help humans create marvelous products on at massive scale. However, the level of precision was still not that impressive, as the majority of the processes were still done by hand.
Compression molding, a production method that predates injection molding, is where there is a consistent shape and size between parts. In this process, engineers would use molds, a compression machine, and a stock to create products that look exactly like the mold. The compression machine pushes the stock into the mold, thus creating the finished products. The level of precision in this process is impressive, and that helps to advance modern society even further.
Injection Molding and Absolute Precision
As the world reached the near-modern era, inventions such as automobiles and skyscrapers changed human societies in just a few centuries. These complex machineries require parts with an extremely high level of consistency as well as reliability. Compression molding alone cannot handle this, as it cannot work with durable metal materials and complex parts.
Injection molding is the key to solving this issue. By injecting the molten materials into the mold instead of crushing the stock above it, injection molding delivers high-quality parts with impressive complexities. It can also be scaled up to mass-produce parts with relative ease to help you complete bulk orders.
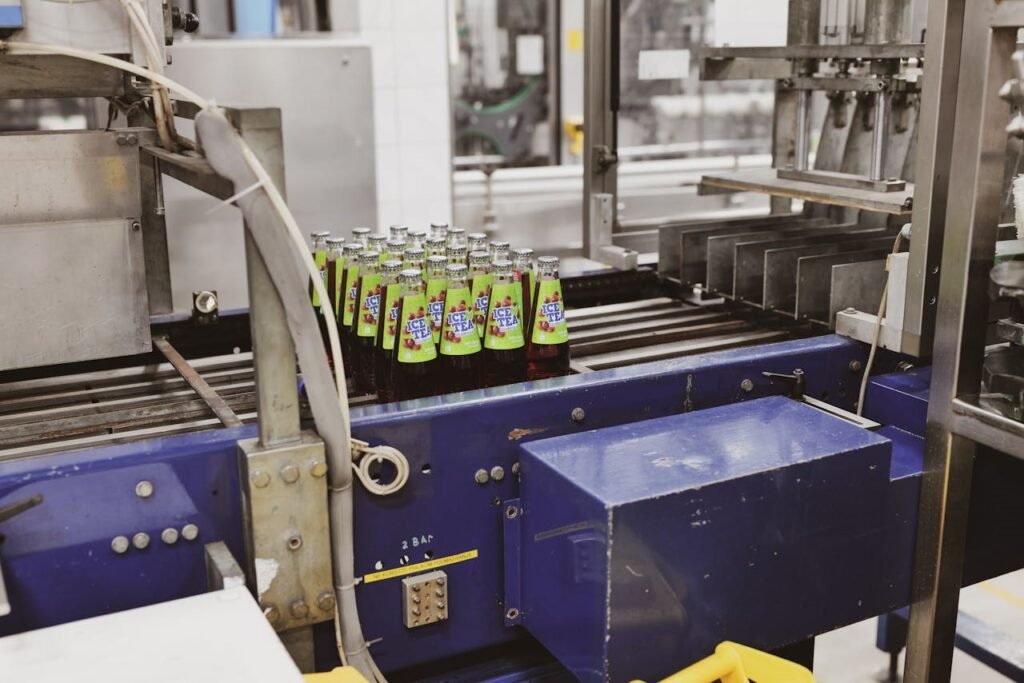
As a concept, injection molding was first conceptualized in the 19th century, and the first ever injection molding machine was made in 1872 in the USA. It was relatively simple compared to the modern injection molding machine. It only consisted of a plunger that pushed thermoplastics into a heated metal tube leading to the mold. The tube would melt the plastic and the mold would shape it. Naturally, due to the simple design of this machine, it was only used to create simple products or parts such as hair combs and buttons.
The first breakthrough came in the 1940s, during World War 2. The need for cheap and inexpensive products that could still match high standards was a pressing matter during this period, so manufacturers were scrambling to find a way to fill this increased demand. In 1946, an inventor named Hendry invented the first-ever screw injection molding machine, which offered engineers an even better degree of control over the amount of molten products poured into the mold, adding more precision to the process. This machine also marked the first time manufacturers can add mixtures of molten materials into the molds, resulting in colored finished products as well as mixtures that have better durability and reliability as a whole.
Hendry would go on to improve the process even further with another breakthrough. In the late 1970s, he developed gas-assisted injection molding machines, which enabled manufacturers to produce high-quality parts with complex designs as well as articles. This invention improved the flexibility of the production method, and soon, its popularity exploded. At the same time, plastic production gradually replaced steel production as the premier choice for manufacturers, so many industries switched to injection molding for the extra precision.
Which Industries Employ Injection Molding the Most?
While most industries would clearly benefit from injection molding, some gain a lot more than others. Industries that require a high degree of precision such as medical devices, automotive, and construction gain a huge boost through injection molding, as the production method enables manufacturers to complete bulk orders with ease.
The automotive and airplane industries are two particular benefactors of the technology. Car accidents or airplane accidents are very serious issues, so every single part must fit with one another to prevent any tragic accidents.
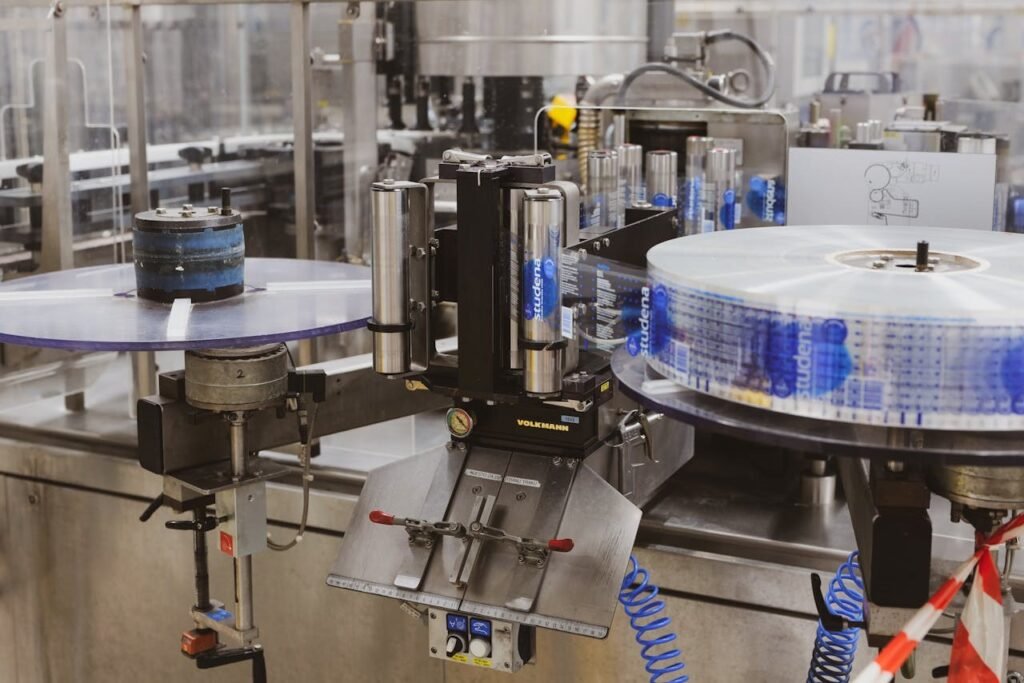
The Importance of Plastic Injection Molds
Plastic Injection molds are the most important component of the entire injection molding process. The mold decides the shapes and sizes of the finished products, and if there is only a single defect from the mold, it is likely that your entire production line is affected. Thus, you should only buy plastic injection molds from true experts in the field.
With over 20 years of experience handling injection molding production for various clients, KuiXing Shanghai offers not just the best expertise in the field but also top products that last for ages. For more information about our range of plastic injection molds, don’t hesitate to contact us right away!
Injection molding is a huge leap in precision in production, as this method enables manufacturers to control a lot of different parameters. The method also uses a wide range of different materials, which makes it a lot more flexible than compression molding or other production methods of the same kind. The automotive industry and the medical device industry are among the top industries that gain the most from the precision level that injection molding offers.
References:
https://www.britannica.com/technology/hand-tool/Neolithic-tools