Contents
Compression Molding Materials
What is Compression Molding?
Compression Molding Materials
Bakelite
Polypropylene
Epoxy
Sheet Molding Compounds (SMC)
When to Choose Compression Molding?
Is Compression Molding Better than Injection Molding?
How to Find the Best Plastic Injection Molds?
Conclusion
If you have ever thought that destruction never leads to creation, compression molding would like to have a word with you! An age-old and reliable production process, compression molding still enjoys considerable growth even full centuries after its introduction, a testament to how timeless it is.
However, starting a manufacturing business with compression molding is deceptively difficult. Even though it comes with low initial costs, maintaining the production line is a major challenge that businesses have to overcome. The key to this issue lies in the compression molding materials. Understanding them will enable you to run a successful manufacturing business.
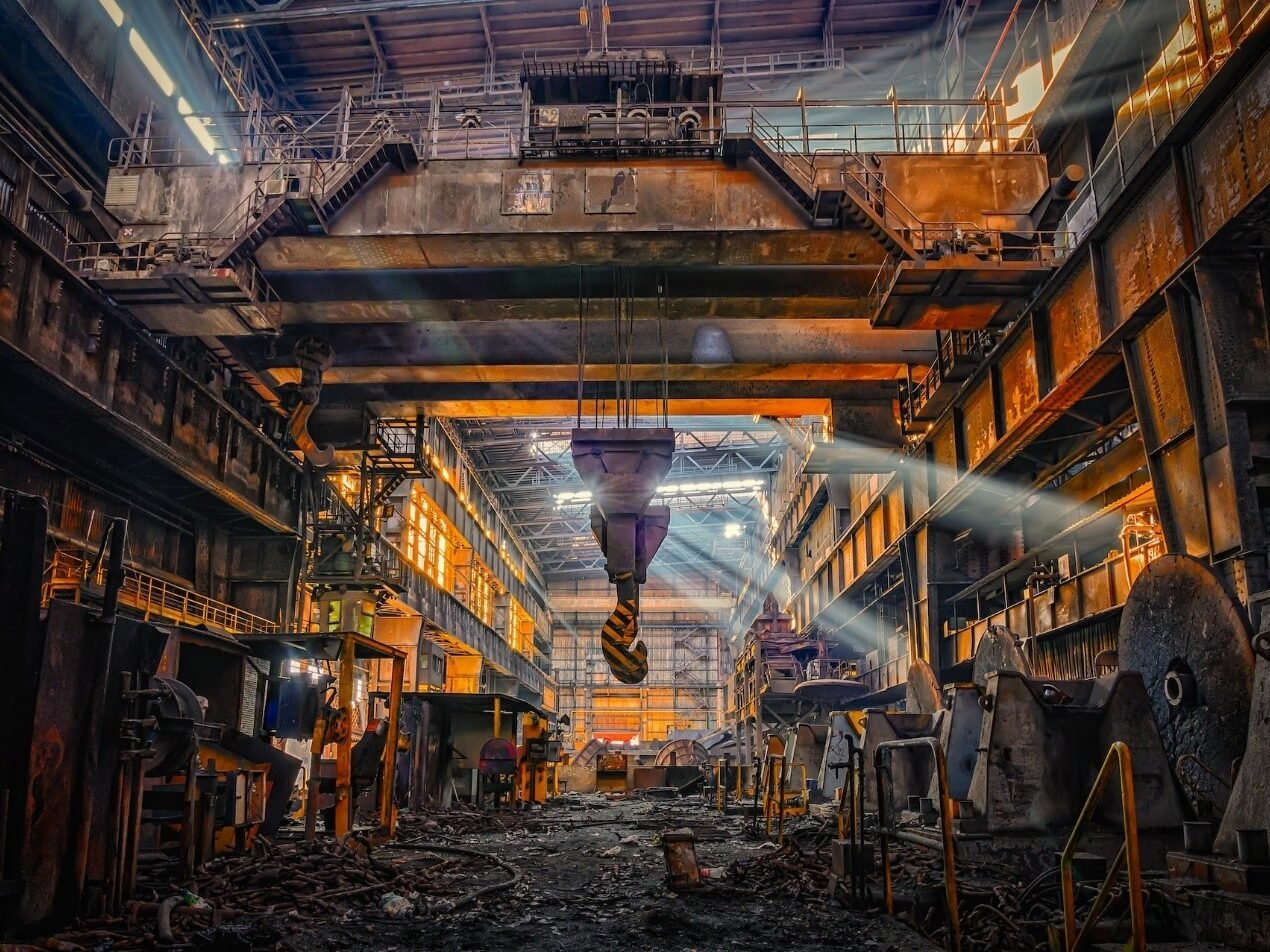
What is Compression Molding?
Compression molding is a timeless production method that first appeared in the early 1900s, and it is still relevant today, though not to its past extent. In this method, engineers prepare a mold, divided into two parts, the upper and the lower part, and the charge, which is typically made from malleable materials. They then put the pre-heated charge inside the mold and use a compression machine to press the two parts of the mold down, crushing the charge and forcing it to take on the shape of the mold.
When the charge is being formed, some excess material will leak out of the mold. Industry experts call them flash, and the engineers will have to remove the excess flash before taking out the finished product.
Compression Molding Materials
As the process demonstrated, compression molding can only work with highly malleable materials, most of which are thermoplastics and thermosetting materials. Compression molding does not work with materials or glass materials.
Thermoplastics are plastic materials that soften considerably when heated and then harden rapidly when cooled down. These materials are extremely malleable, and they can be reshaped as well as reheated numerous times without breaking down. They can also be used in the more modern injection molding process.
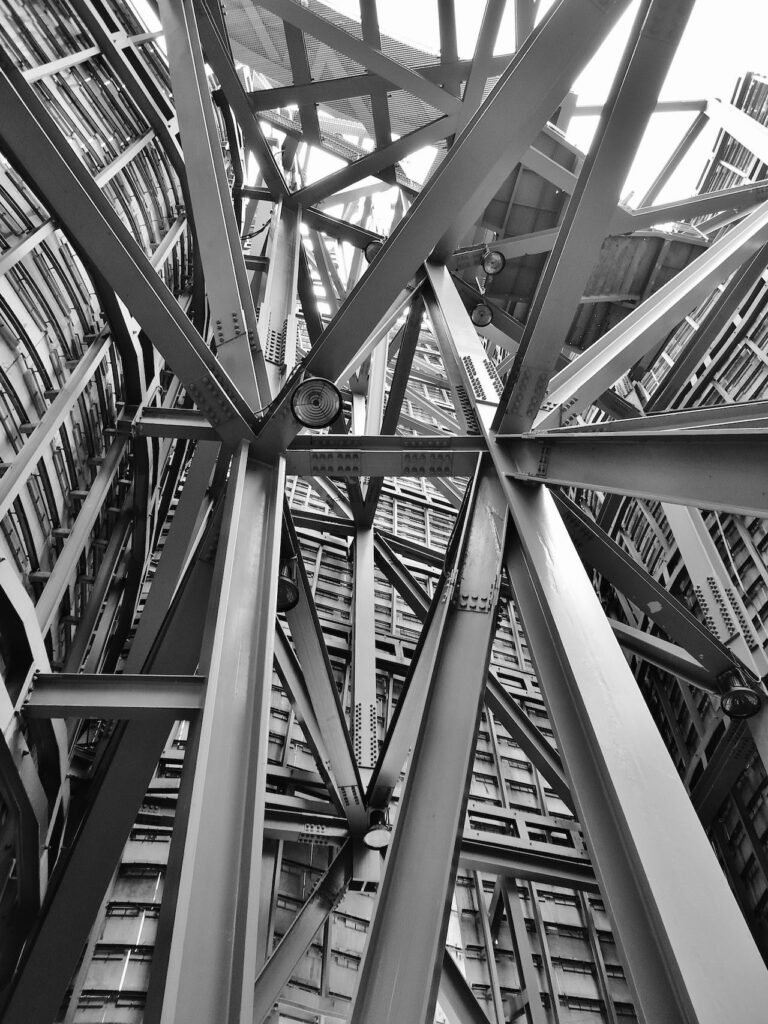
exposed to heat, they are irrevocably cured, which essentially means you can only shape them once. These materials are typically compounds, as they contain coloring agents or catalysts. Thermosets are generally tougher than thermoplastics.
Bakelite
Bakelite is the original material that led to the creation of compression molding and propelled the development of the industry as a whole. Bakelite is a kind of thermosetting resin that features high malleability and electrical non-conductivity, making it a great choice for compression molding.
During the compression molding process, Bakelite charges can be removed from the process without the need for coolants, speeding up the process considerably.
Polypropylene
The second-most produced plastic material after polyethylene, polypropylene is a thermoplastic material characterized by its high heat resistance and flexibility, enabling it to be the base material for just about any consumer good possible. Polypropylene is also resistant to fatigue, so the finished products made from this material can last for generations with ease.
Epoxy
Epoxy is a class of materials made from epoxy resins, also known as polyepoxides. This kind of material features strong chemical and corrosion resistance, as well as high compression strength and adhesion. In compression molding, epoxy resins are usually added to other compounds to make thermosetting materials with unique properties. Epoxy is generally used in electronics, electrical components, and composites.
Sheet Molding Compounds (SMC)
SMC is a material specifically designed to be used in the compression molding process. Produced by reinforcing polyester materials with fibers, SMC features great durability and flexibility, but the aesthetics of the material leaves a lot to be desired. Where it shines is the amazing production volume associated with it. SMC enables manufacturing plants to semi-automate compression molding and greatly reduce labor costs as well as efforts, making it the perfect choice for your compression molding business.
When to Choose Compression Molding?
Compression molding, in spite of its age, is still a reliable production method, and the industry is still researching new materials as well as catalysts to improve it. However, it is not a one-size-fits-all solution.
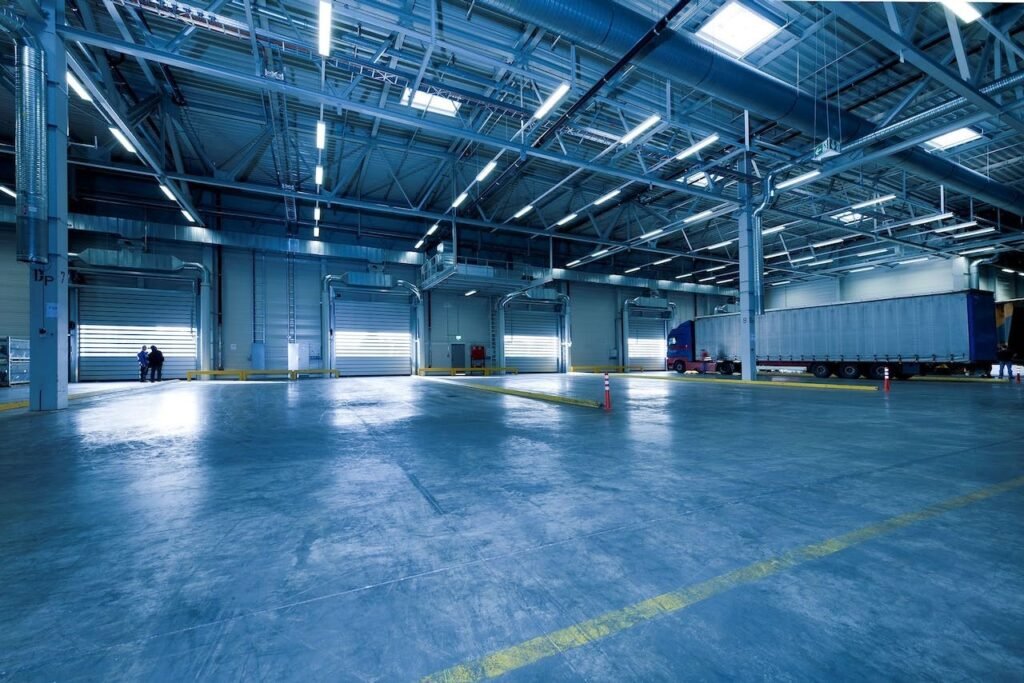
Compression molding is great when you need to produce low-to-medium volumes of products, as the process has a long cycle and requires some bits of manual labor. You should also take into consideration the fact that compression molding can only take on simple products and that it does not work with metal materials. For this reason, compression molding is not popular in industries such as aircraft parts manufacturing, automotive, and medical device manufacturing.
Is Compression Molding Better than Injection Molding?
Injection molding is a more recent production method that is developed from compression molding. Injection molding works by injecting molten materials into a pre-cast mold to help it take on the form of the mold.
Due to how it works, injection molding is far superior to compression molding in producing complex parts with different chambers as well as holes, provided that you have prepared the right mold design. Injection molding also works particularly well with metals, thermoplastics, and glass materials. Finally, injection molding features amazing scalability, enabling you to fulfill high-volume orders with ease.
How to Find the Best Plastic Injection Molds?
The most impactful downside of injection molding is the initial set-up costs. Injection molding tools and machines can be quite expensive, and getting the right plastic injection molds means that you have to work with the top professionals in the field to deliver consistent results. The costs can be offset by finding the right long-term partner to work with you over long periods of time.
Conclusion
Compression molding materials include thermoplastics and thermosets, the most prominent of which include Bakelite, Polypropylene, epoxy, and SMC. Compression molding does not work with metals or glass materials due to how inflexible these materials are without the right heat treatment.
Compression molding is not necessarily better than injection molding. For starters, it cannot handle complex parts due to simplistic mold design. It is also restricted by materials, which are strictly plastics or resins, and it cannot produce parts fast enough to complete high-volume orders. In these scenarios, injection molding remains the superior choice thanks to its flexibility and amazing scalability.
References:
1-https://www.linkedin.com/pulse/compression-molding-machine-market-size-2023/
2-https://link.springer.com/chapter/10.1007/978-1-4615-7604-4_9