Outline:
- Introduction
- What is the importance of plastic mold designs?
- Design Considerations for Injection Molding
- Thickness of the wall
- Ribs
- Sharp vs curved corners
- Draft angle
- Bosses
- Textures and lettering
- Undercuts
- Inserts
- Chose Kuixing Electronics for your Injection molding design
- Conclusion
Introduction

About a century ago, the very first injection molding press was developed. The device was simple but effective, and it resulted in an industry that would permanently alter the manufacturing process. When compared to alternative manufacturing methods, injection molding can sometimes be less expensive while maintaining a wide range of sophisticated material qualities.
Designing your product for injection molding is key to realizing these benefits. You’ll also discover that properly developing your item will result in a balance of best results and value for money. The following material provides an overview of the most significant elements for injection molded parts, drawing on both generic injection mold design standard procedures and decades of personal expertise. This article will guide you on how to design a mold for plastic injection molding.
What is the importance of plastic mold designs?
Designing your molds for your specific and unique product has a lot of benefits. Mainly a proper mold design can drastically lower the cost of processing each part. In the designing process we follow best practices that develop long lasting molds, reduce undercut ratio, makes the process of selection material easier, and creates series or multi-cavity molds to decrease costs.
If the design, material selection, and other factors are optimized, the process of injection molding becomes quicker and results in greater production rate per cycle. As a result the cycle length is reduced, that means more parts are produced per hour.
If a mold is not designed well, it can cause many issues that can negatively impact the manufacturing process, including: increased processing cost, inconsistent product quality, decline in productivity, and visual defects etc.
Best practices for designing Injection Molds

There are a lot of factors to have in mind for injection mold design, some of most important ones are:
Thickness of mold walls
The less thick it is, the simpler the injection molding process. Parts with thin walls cool faster, weigh less, and use less plastic per part. This leads to faster cycle times, more components produced per hour, and cheaper manufacturing costs.
Injection molded pieces typically have a wall thickness ranging from 0.08″ (2millimeters) to 0.16″ (4millimeters), but can be as thin as 0.02″ (0.5millimeters). However, wall thickness varies according on the material utilized.
Wall thickness must be uniform to minimize, if not eliminate, warping. If consistency is difficult to achieve due to design constraints, the thickness modification should be implemented gradually. Using a coring process and inserting gussets can assist eliminate such issues.
Ribs
Rather than increasing the thickness of the wall, ribs are commonly employed to improve a part’s bending stiffness, which is caused by a boost in the moment of inertia.
When installing ribs, keep in mind that the thickness should not exceed 60% of the nominal width, and the draft angle should be at least 0.25 degrees.
Sharp vs curved corners
Sharp corners in the template will result in molded-in stress when the resin flows. A stress riser can also occur during application. However, round corners have the opposite effect: they reduce stress concentrations and breakage. For efficient injection molding, the inner perimeter should be at least as thick as the walls.
Draft angle
When molded pieces are difficult to expel, drag marks or ejector punch marks may appear. To aid speedier ejection, apply a draft angle of 1°-2° to all walls perpendicular to the clamping unit’s separating direction. If design constraints do not allow for draft angles, a side motion mold may be essential.
Bosses
Bosses are used to attach fasteners like screws or receive threaded inserts. They primarily facilitate the registration of mating parts. Good bosses should not have large sections, which can cause sink and voids in injection molded parts.
Keep in mind that the thickness of the Bosses’ wall should not exceed 60% of that of the main wall. Additionally, the base radius should be at least 25% of the thickness of the main wall.
Textures and lettering
Textures and inscriptions can be added to a part for aesthetic or branding purposes. Texturing is also an excellent method for concealing surface flaws and other irregularities on a molded object. Textures and writing, like everything else in moldability design, follow criteria.
The extra draft must be applied to textures and characters with limited depth. This allows for part disassembly without dragging or causing marks. In general, texturing must have a minimum depth of 1.5° per 0.025millimeters (0.001 inches) in addition to typical draft.
However, these statistics may vary based on the part being made. Laptop devices, for example, have an internal texture depth of 0.025 millimeters (0.001 inches), requiring a draft of 1.5°. Leather with a depth of 0.125 millimeters/0.005 inches, on the contrary hand, demands a draft of at least 7.5°.
Lettering calls for using a font size with the tiniest feature, such as Sans Serif. Serif typefaces measuring a minimum of 0.020 inches thick are acceptable.
Undercuts
These are pieces of the design that prevent the mold from sliding away along the parting direction. It’s either exterior (protrusion) or interior (depression). Unless absolutely required, external and internal undercuts should be kept to a minimum. If necessary, a feature should be redesigned. Otherwise, tooling costs will rise because external undercuts require side cores, but internal undercuts necessitate internal core lifters.
Inserts
These plastic pieces allow fasteners, such as screws, to be put and replaced repeatedly, allowing for a longer time setup and breakdown cycles. This is particularly true for inserts crafted from brass. Insertions are often inserted in injection molding parts utilizing ultrasonic insertion, heating insertion, or molded-in.
Whatever the case, exterior threads must be perpendicular to the separating direction, as setting them parallel will necessitate the use of an unscrewing mechanism, increasing tooling costs.
Chose Kuixing Electronics for your Injection molding design
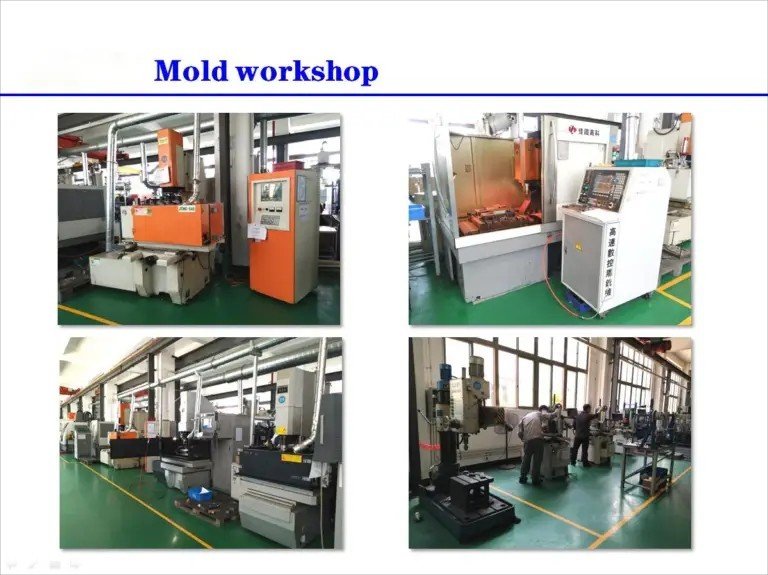
Given the numerous aspects of design for injection molding, applying all of them and producing the correct product requires specialized skills, training, and expertise. This is something only professionals can do, and Kuixing Electronics has a large number of them available.
As a source of skilled engineers and product designers, we can supply you with an individual or a team of professionals to assist you in developing injection mold and parts from the beginning. We will link you with pre-screened, highly competent design specialists.
Request a quote today and tell us about your project!
Conclusion:
In conclusion, designing a mold for plastic injection molding is a crucial aspect of the manufacturing process that significantly influences cost, efficiency, and product quality. The importance of plastic mold designs lies in their ability to reduce processing costs, enhance material selection, and optimize production rates. Factors such as wall thickness, ribs, corners, draft angles, bosses, textures, undercuts, and inserts play pivotal roles in achieving a successful injection molding process.
Adhering to best practices in mold design, including considerations for wall thickness uniformity, appropriate use of ribs, avoidance of sharp corners, and implementation of proper draft angles, ensures optimal outcomes. Kuixing Electronics emerges as a reliable choice for injection molding design, boasting a team of skilled engineers and product designers capable of navigating the complexities of mold design.
In the dynamic landscape of injection molding, where precision and expertise are paramount, choosing a professional partner like Kuixing Electronics can streamline the design process, reduce costs, and deliver high-quality results. With a focus on specialized skills, training, and experience, Kuixing Electronics stands as a valuable resource for those seeking efficient and effective injection molding solutions.
External links:
https://www.google.com/url?sa=t&source=web&rct=j&opi=89978449&url=