Contents
How to Reduce Shrinkage in Injection Molding
What is Shrinkage in Injection Molding?
3 Ways Mold Shrinkage in Injection Molding Can Ruin Your Workflow
Preparing for Mold Shrinkage in Injection Molding
5 Ways to Reduce Mold Shrinkage in Injection Molding
Adjust Materials’ Temperature
Adjust the Mold’s Temperature
Apply Strong Injection Pressure
Reduce Wall Thickness
Immerse the Parts in Cold Water
How to Prepare the Perfect Plastic Injection Mold?
Where to Find the Best Plastic Injection Mold?
Conclusion
For business owners looking to scale their production massively, injection molding is the process of choice. Featuring a highly automated process with amazing scalability, injection molding enables you to fulfill high-volume orders with relative ease. As breakthroughs in the field are coming in at a breakneck pace, even non-experts can dive into injection molding with ease now.
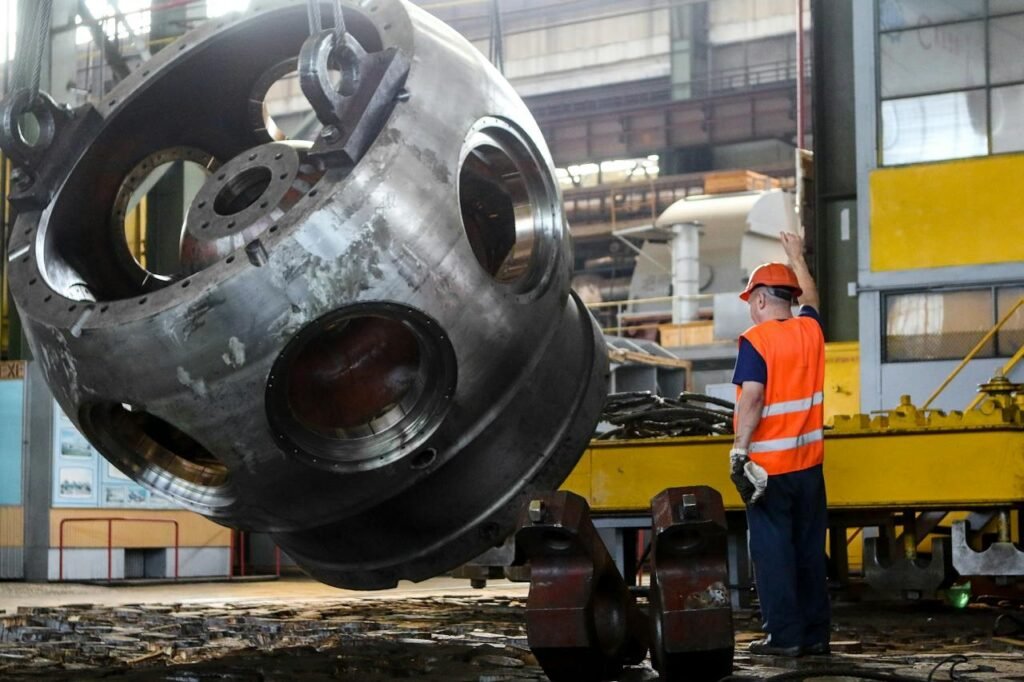
One of the most persistent issues that injection molding businesses encounter is mold shrinkage. This major issue can cause disruptions in your workflow, costing you hundreds of thousands. Thus, reducing shrinkage in injection molding is a top priority for any business.
What is Shrinkage in Injection Molding?
When thermoplastic materials are melted and then solidified, a portion of the materials will be lost in the process. As a result, the finished products will not have the same dimensions and volume as the input material. This event is called mold shrinkage.
Mold shrinkage does not happen equally to all materials. Some materials come with naturally high shrinkage such as nylon, while others, mostly ABS materials, have low shrinkage in general.
3 Ways Mold Shrinkage in Injection Molding Can Ruin Your Workflow
Mold shrinkage causes loss during the injection molding process, so it is to be avoided if possible. Here is how mold shrinkage causes disruptions to your workflow:
- Mold shrinkage costs money: Any lost material during the injection molding process costs you money. When this amount accumulates over time, it can become a huge expense.
- Mold shrinkage costs you contracts: When mold shrinkage occurs, some of the parts produced by your business may not satisfy the strict requirements set out by your client. Thus, you may lose high-value contracts that can make or break your business.
- Mold shrinkage may cause real-life accidents: Injection molding is generally used to create automotive parts or airplane parts, which have to be exactly the same as the blueprint, down to millimeters, for safety reasons. If the parts were shrunk, they might not fit with one another as intended, causing real risks to drivers.
Preparing for Mold Shrinkage in Injection Molding
As mentioned before, each thermoplastic material comes with a different mold shrinkage rate. For this reason, one smart way to prepare for shrinkage in injection molding is to find the appropriate material for your project. As an example, nylon materials might be cheaper, but they generally feature very high shrinkage rates, so they will cost quite a lot in the long run.
To find the exact shrinkage rate for each material you are interested in, get a mold shrinkage chart. This chart should contain all the shrinkage information you need to pick the perfect material for your project.
5 Ways to Reduce Mold Shrinkage in Injection Molding
That said, minimizing mold shrinkage should still be a top goal for your production line. Here are some common methods to reduce mold shrinkage.
Adjust Materials’ Temperature
The first key lies in adjusting the temperature of your molten materials as you work with them. The general rule of thumb is to lower the temperature as you pour the molten materials into the mold, which helps to minimize molecular expansion. This will effectively prevent shrinkage in the cooling phase.
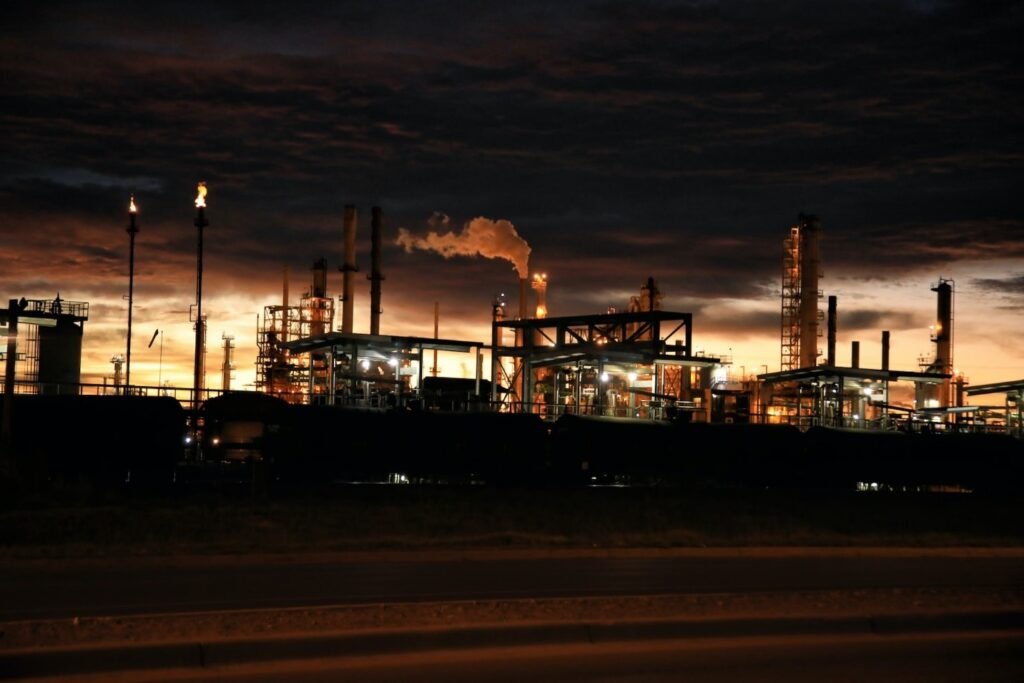
Adjust the Mold’s Temperature
The temperature of the mold itself throughout the injection molding process can also have a huge impact on the overall outcome. Before starting the process, heat up the mold so that the molten materials can fill all compartments within the mold with ease, ensuring that mold shrinkage will be kept at a minimal level.
Apply Strong Injection Pressure
The idea behind this method is to inject the molten materials with strong pressure. This will enable them to quickly fill the mold cavity, reducing mold shrinkage. However, you have to be careful with this method: Too much pressure could cause damage to the mold or even destroy it outright.
Reduce Wall Thickness
You can add a bit of shrinkage control during the mold design process. By designing parts with thinner walls, you can reduce mold shrinkage considerably, as the materials will not need as much time to cool down, resulting in less shrinkage. This is a very dangerous double-edged sword, however, as having thinner walls means that the parts are going to be more fragile.
Immerse the Parts in Cold Water
This is a helpful method to control the temperature during the cooling process. By immersing the parts in cold water, they will cool down much more quickly, resulting in less shrinkage. Naturally, it comes with a tradeoff: The stress from the instant cooling process may cause structural damage to your parts.
How to Prepare the Perfect Plastic Injection Mold?
Designing a great plastic injection mold is the first step for a sustainable and profitable injection mold business. The mold is where the magic of injection molding happens, so it is important to get the best plastic mold in the first place. A good mold can help you deal with common issues such as shrinkage, ensuring that your business can thrive.
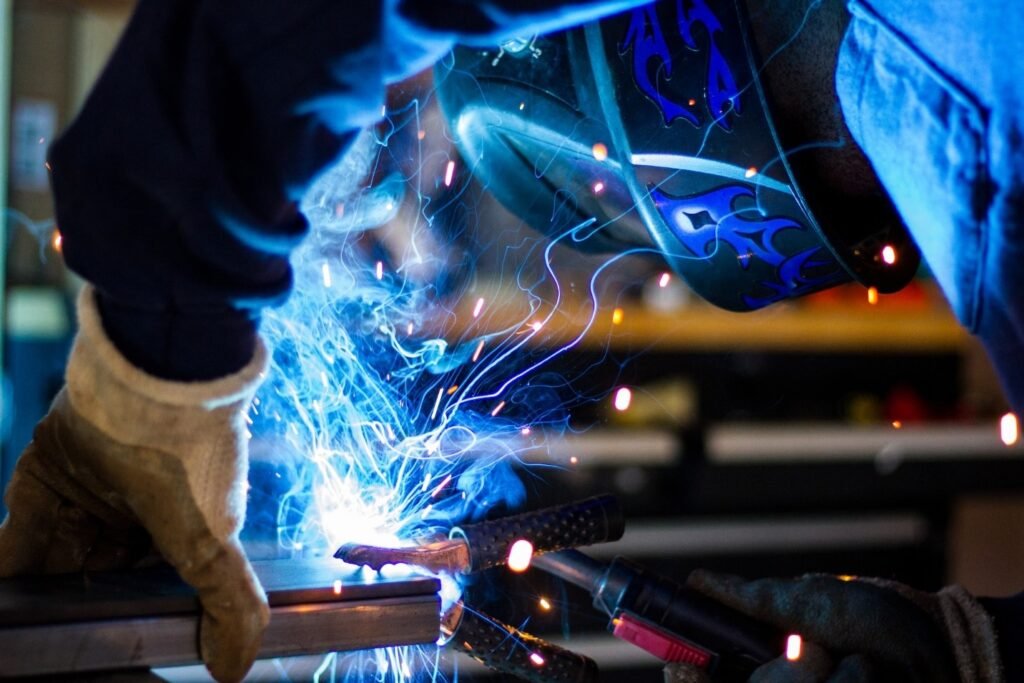
Where to Find the Best Plastic Injection Mold?
With over 25 years of experience in the field, Shanghai Kuixing delivers high-quality injection molds and injection molding tools to help your business get started. Our mold design experts understand the specific business needs you have to take into account, which enables them to create high-quality injection molds that do not compromise the quality. We are happy to help your business scale.
Conclusion
There are five main ways to reduce shrinkage in injection molding: adjusting materials’ temperature; adjusting the mold’s temperature; applying strong injection pressure; reducing wall thickness; and immersing parts in cold water. All of these methods are highly effective, but they come with high prices that should be regulated carefully if you wish to retain the integrity of the parts.
Getting the most efficient mold design is often the best way to reduce mold shrinkage, as you will not have to worry about structural damage. Contact our experts at Shanghai Kuixing now if you have inquiries about our services.
References: