Contents
Low-Pressure Injection Molding
What is Low Pressure Injection Molding?
Why Choose Low Pressure Injection Molding?
Benefits and Downsides of Low Pressure Injection Molding
Benefits
Downsides
When Should You Choose Low Pressure Injection Molding
Plastic Injection Mold
In the modern era, the need to make high-quality parts at scale to meet the massive consumption demand of end clients (There are as many as 16 billion injections administered each year). If manufacturers wish to take on these massive orders and catch up with the growth in the industry, injection molding is a reliable choice.
As the injection molding industry grows, so does the technology involved in the field. Low-pressure injection molding is a great technology that enables manufacturers to cut down on costs considerably without needing extensive operation process redesigns.

What is Low Pressure Injection Molding?
Low pressure injection molding is a new variation of injection molding. The principle is the same: You inject molten materials into a mold, which fills the mold. When the materials cool down, they take the shape of the mold, creating the finished product.
For low pressure injection molding, there are some changes in the process for better performance and efficiency. In this process, engineers would inject molten materials, mostly polyamide materials with strong adhesiveness, into the mold with low pressure. The mold is also not a conventional mold as in conventional injection molding. It contains electrical circuits or sensitive electrical boards that might get damaged or destroyed in the case of conventional injection molding. In low pressure injection molding, however, the molten materials will quickly form a protective layer surrounding the board. Engineers will then take out the finished product, polish it, and put it to the next step.
Why Choose Low Pressure Injection Molding?
Low pressure injection molding is a great method of production when you need to protect the items inside the mold itself. Think USBs, medical devices, electrical boards, etc. Because the pressure from the injector is not very high, risks of damaging the parts are kept at a minimal level. Furthermore, low pressure injection molding as a method does not use conventional thermoplastic materials, which can be quite toxic and non-recyclable.
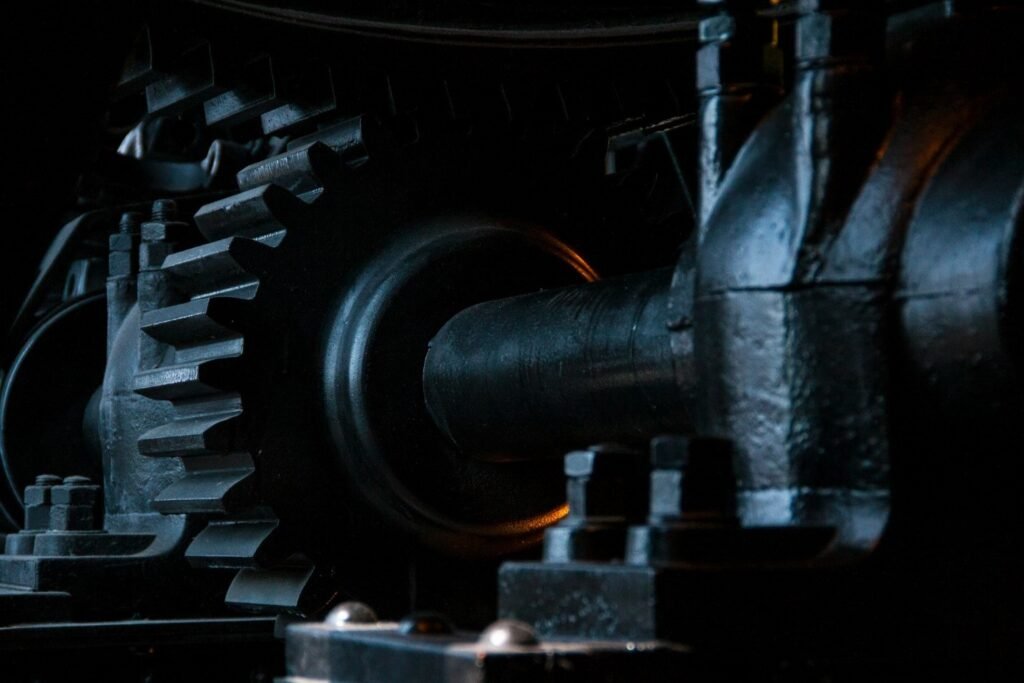
Benefits and Downsides of Low Pressure Injection Molding
Adopting low pressure injection molding helps you to take your business to the next level, but there are some potential risks and downsides you have to take into account.
Benefits
The biggest benefit of adopting low pressure injection molding is the capability to handle highly complex projects involving electrical engineering. With low pressure injection molding, you can mass-produce military-grade connectors, USB devices, and much more. These orders are worth millions of dollars, so they are well worth the investment.
Low pressure injection molding is also more energy efficient, as it does not use an enormous amount of energy to run the production line.
Finally, as noted above, materials used in low pressure injection molding are more eco-friendly than the ones used in conventional injection molding.
Downsides
Perhaps the biggest downside of this method is the sheer cost of starting a new production line. Low pressure injection molding isn’t exactly a new method, but it does come with a lot of preparations, so you have to invest in new machines and an entire new production line. They certainly don’t come cheap.
You will also need highly trained personnel for low pressure injection molding, as the process takes a bit more work than conventional injection molding. Finding the right workers and engineers for this niche might be quite difficult.
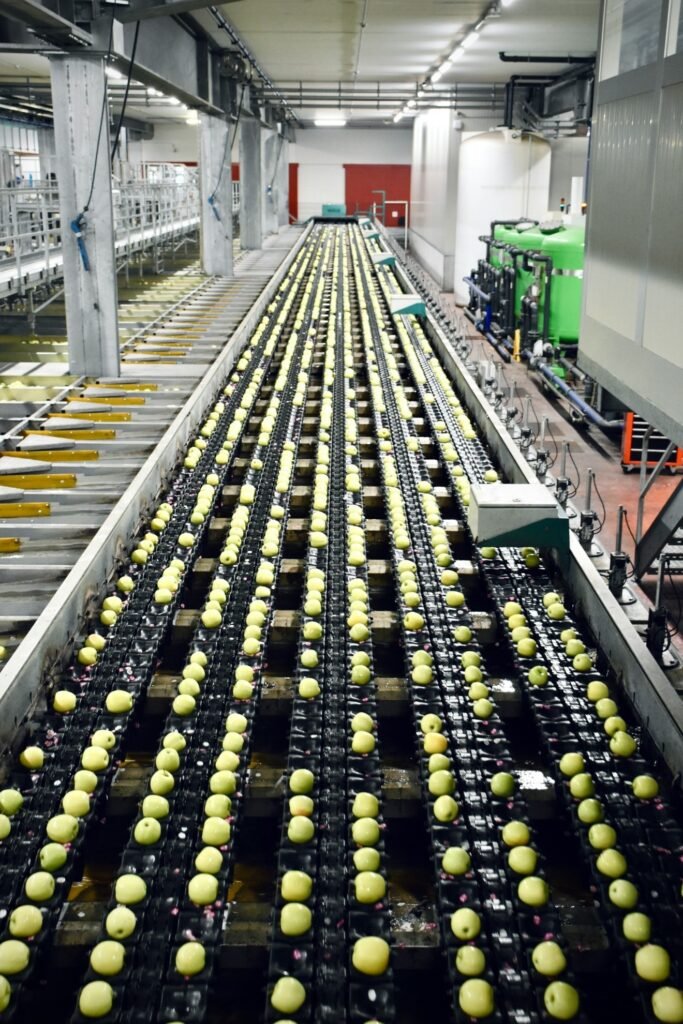
Finally, since low pressure injection molding is very restrictive in terms of materials, you cannot use cheap thermoplastic materials to cut down on costs, inflating production costs even more.
When Should You Choose Low Pressure Injection Molding
When you have a strong R&D team with good technical knowledge, starting a low pressure injection molding production line will become much more realistic. The R&D team will need some time to figure out the perfect pressure level to use for this line, so it is a good idea to give them plenty of breathing room.
Furthermore, you will have to work with good suppliers who can provide a wide range of high-quality polyamide materials on a regular basis. Nothing is worse than running out of materials when you need to complete a massive bulk order with very little time to spare.
With all the two factors above taken care of, now you just need to make sure that you have contacts in the niches that greatly value low pressure injection molding. This method is highly valued by the military industry, automotive, consumer products, medical devices, and unique products. That’s a lot to do, but when you have proved your worth, your business will thrive for years to come.
Plastic Injection Mold
If you can’t take on low pressure injection mold, it is totally fine. Conventional injection mold is more than capable of handling bulk orders as well. This method is also highly scalable, so you can easily scale back or up the production when needed. It is the premier choice for most manufacturers out there!
The most important part of a plastic injection molding production line is the plastic mold itself. The plastic mold needs to be precise and accurate to the T, otherwise defects will carry down to all products in the production line. To make sure that you get nothing but the best plastic injection mold, contact our experts at KuiXing Shanghai. We have over 23 years of experience producing plastic injection molds, and we can’t wait to help you get started with the best plastic injection mold, whatever your niche.
Low pressure injection molding is a modern variation of injection molding, where the materials, most often polyamide materials, are injected slowly and at low pressure into the mold cavity. Inside the mold cavity are fragile electrical boards or circuits, which cannot withstand high-pressure injection. Thus, low pressure injection molding will create a protective layer surrounding these boards, protecting them from harm. After the injection is done, the engineers will carefully take out the finished products and put them through a cooling process. Low pressure injection molding is much more efficient and environmentally friendly than conventional injection molding, but it is also more expensive to set up.
Reference:
https://www.who.int/news/item/23-02-2015-who-calls-for-worldwide-use-of-smart-syringes