Outline:
- What is plastic injection molding
- Injection Molding machine
- The process
- Injection Molding material
- Conclusion
What is plastic injection molding
The injection molding process is a manufacturing technology that enables large-scale production of items. It operates by pumping molten materials into a mold (or ‘mould’ in the United Kingdom). It is commonly used as a large-scale manufacturing method to create thousands of similar things. Metals, glasses, elastomers, and confections are among the materials that can be injected molded; however, thermoplastic and thermosetting polymers are the most frequently used materials.
Now you might be wondering how this process works. So in today’s article we’re going to walk you through the process of plastic injection molding that we use here at Kuixing Electronics.
Injection Molding machine

An injection molding machine is separated into two units: a clamping unit and an injection unit. The clamping unit’s functions include releasing and locking a die and ejecting goods. There are two sorts of clamping techniques: the toggle type, as shown in the image below, and the straight-hydraulic style, in which a mold is opened and closed using a hydraulic cylinder. The injection unit’s functions include melting plastic with heat and injecting the hot plastic inside a mold. The screw is turned in order to melt plastic fed from the hopper and gather molten plastic in front of the screw (a process known as metering). After the requisite amount of molten plastic has been accumulated, the injection procedure begins.
While molten plastic flows through a mold, the machine controls the screw’s movement speed, also known as injection speed. On the other side, it regulates dwell pressure once molten plastic fills cavities. The transition from speed control to pressure control is programmed at the time where either the screw position or the injection pressure reaches a predetermined value.
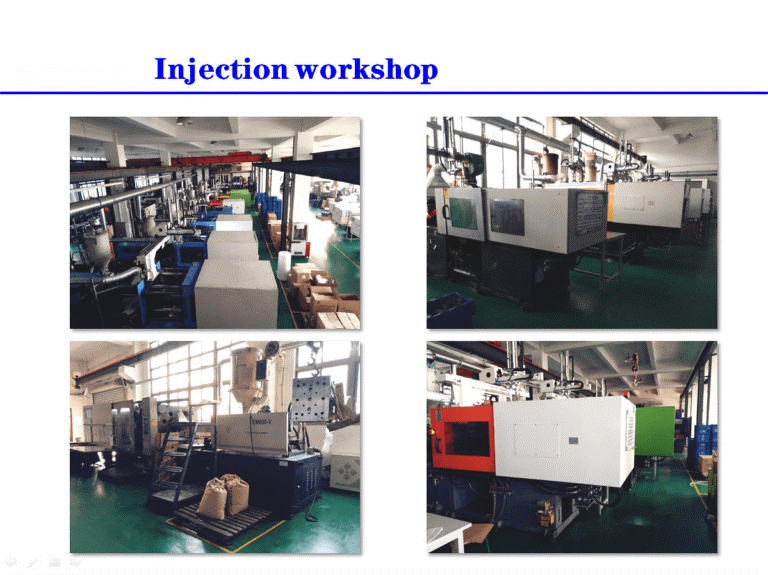
The process
Injection Molding is a very quick and streamline process..
Creating the product design, tooling a mold to fit the design, melting plastic resin pellets, and applying pressure to inject the melted pellets into the mold are the fundamental steps in the plastic injection molding process.
Here’s a breakdown of each step:
1.Clamping
The initial step in the injection molding method is clamping. Injection molds are often designed in two clamshell-style parts. In the clamping process, the mold’s two steel sheets are pressed together in an automated press.
2. Injection
When the two mold plates are fastened together, injection can commence. The plastic, which is usually in the form of grains or pellets, which are is first melted into a full liquid. Then the liquid is pumped into the mold. Producers should ensure that the temperature remains steady during this stage of the process.
3. Melting
During the dwelling phase, plastic that has been melted completely fills the mold. Force is applied directly to the mold to guarantee that the liquid fills every opening and the finished product is similar to the mold.
4. Cooling.
The cooling phase is the simplest; the mold should be set aside until the hot plastic within has cooled and solidified into a useable product that can be safely withdrawn from the cast.
5. Mold opening.
Once the item has cooled, the clamping motor will gradually open the two sections of the mold to ensure a safe and proper removal.
6. Ejection
With the mold open, an ejector bar progressively pushes the hardened product out of the open mold chamber. The maker should then utilize cutters to remove any excess material and finalize the finished product for client use. Waste products can frequently be recycled and injected again into the next component, lowering your material expenditures.
Given the length of time and expense of equipment, injection molding can be a daunting task. However, after the first mold is formed, injection molding is the simplest way to produce a large number of identical parts at a cheap cost, which is why it is one of the most rapidly expanding manufacturing practices today.
If you want to get started with injection molding, Kuixing is ready to lend a hand. We’re professionals at speeding up the process for generating a precise mold, and we offer exceptional support to every customer throughout the whole production lifetime. Contact us today if you’re ready to start.

Injection Molding material:
Injection molding materials are plastics, specifically thermoplastics. Hundreds of thermoplastics exist, but the most commonly used ones in injection molding are:
Polypropylene, Polyethylene, Acrylonitrile Butadiene Styrene (ABS).
These three thermoplastic materials are used often. They are affordable, long-lasting, and can withstand the strains of frequent use. You most likely use products created from these three materials on a regular basis, if not on a daily basis. ABS, for example, is a polymer used to manufacture the device’s keypad and other components.Other frequent injection molding materials include polycarbonate, nylon, acrylic, and polyoxymethylene. Each of such substances has advantages and downsides, so when deciding which material to employ, consider how the final product will be used. Will it have to be food-safe? Does it need to be heat resistant? Is UV resistant? These are some of the factors to consider while determining which material to employ.
You might need an expert opinion on which material to choose for your specific product, so, if you need any help don’t hesitate to contact us at Kuixing Electronics.
Conclusion:
In conclusion, injection molding machines are complex systems with clamping and injection units working in tandem. The clamping unit secures the mold, utilizing either toggle or hydraulic techniques, while the injection unit melts and injects plastic into the mold through controlled screw movements. The injection molding process involves clamping, injection, cooling, mold opening, and ejection, resulting in the production of identical parts with efficiency and cost-effectiveness. Despite the initial challenges and equipment expenses, injection molding stands out as a rapid and economical manufacturing method for mass production.
External links: