Contents
The Secrets of Cooling System Design in Injection Molds: How to Prevent Part Deformation?
Why is Cooling so Important in Injection Molding
Cooling System Design in Injection Molding
The Secrets to Designing a Top Cooling System
Baffles
Bubbles
Thermal Pins
Some Other Reasons for Part Deformation
Injection molding is quickly becoming the new rising star in the world of manufacturing. It features an impressive compound annual growth rate of 4.74% during the period between 2024 and 2031. As countries around the world demand more and more complex parts with complex shapes and differing dimensions, injection molding will be the premier solution that manufacturers can look forward to.
That said, one major challenge that stands between manufacturers can great success: Cooling time. The cooling time of your injection molding project will be a defining factor of your success, as improper cooling can lead to part deformation. Fortunately, there are some steps that you could take to master the art of cooling system design and prevent part deformation.
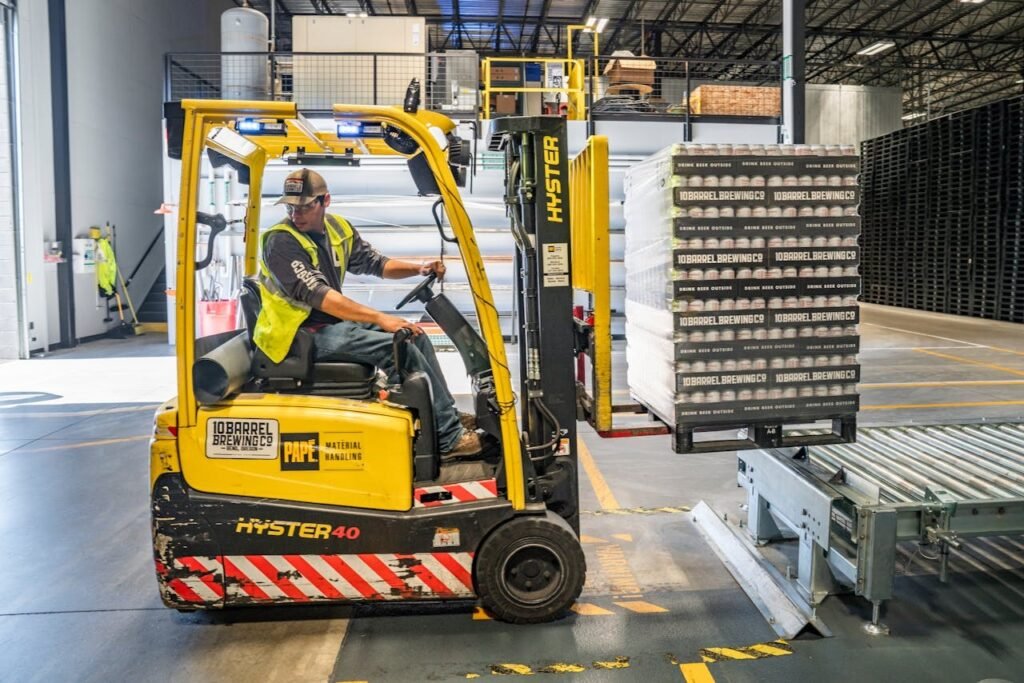
Why is Cooling so Important in Injection Molding
In injection molding, engineers will inject molten materials into a metal mold, and then cool down the materials so that they solidify. After having solidified, the materials will take the shape of the mold itself.
The cooling process is quite important because it can make or break the solidifying parts within the mold. When molten parts solidify, engineers have to take care to apply coolant evenly and consistently across all sides of the parts. If the cooling process happens too quickly, the chance of warpage as well as metal bending increases as well. Thus, engineers have to play a balancing game to ensure the best consistency and efficiency.
Cooling System Design in Injection Molding
In injection molding, there are two popular cooling system designs that you should know about.
Straight-line cooling is the traditional cooling method, where engineers put cooling channels in such a way that water or coolants will run around the mold itself. There will be branch channels as well as side channels to help increase the effectiveness of the entire system. Straight-line cooling is mostly used for production lines that manufacture simple parts or parts with very simple geometry.
A newer cooling method called conformal design is getting more and more popular in some production lines. In this design, engineers would put cooling channels around the twists and turns of the mold cavity. Thus, every single component of the part, no matter how complex the design is, will be cooled down consistently. Conformal design is more popular with complex parts, as there is no room for error in these production lines. One single error could lead to rejection from your partners!
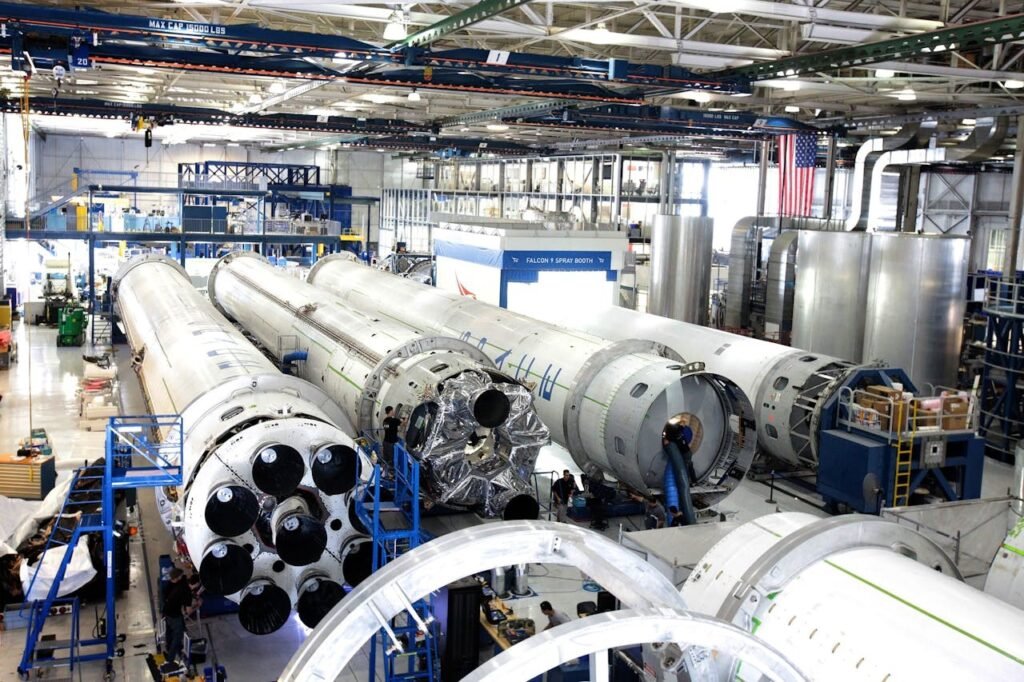
The Secrets to Designing a Top Cooling System
The key to designing a successful cooling system lies in three components: baffles, bubbles, and thermal pins. These are design features available to most engineers, and if you could implement them before starting the production line, you will be able to effectively prevent part deformation and reduce the risks of defects within your production line.
Baffles
Baffles are a design component that helps engineers to cool areas that normally cannot be cooled by the flow of coolants. To create a baffle, engineers would insert a metal plate in the middle of the cooling channel, and then divert the flow upward on one side and then downward on the other. Because the flow will have high flow pressure at the area around the bend, the cooling effect in that area is amplified.
Bubbles
Like baffles, bubbles are design features that help the cooling system cool down twists and turns more effectively. This design involves inserting a tube in the middle of the flow and then connecting one channel to the side of said tube. The other end will be connected to the bottom of the tube. When coolants flow, they will enter the tube and then divert into two flows, one to the top of the tube and the other to the bottom. The top flow will bubble out from the top and then continue the flow to the bottom of the tube. Bubbles are the perfect cooling solution for slender cores.
Thermal Pins
Thermal pins are components that help cool down the mold effectively through the use of condensation. Inside each pin is water or coolant, and the pins are positioned outside the cooling channel at first. When the cooling process starts, they will be inserted into the channel to help draw away the heat. High heat will vaporize liquid inside the pins, which then condenses. Thus, the cycle is then repeated until the desired temperature is reached.
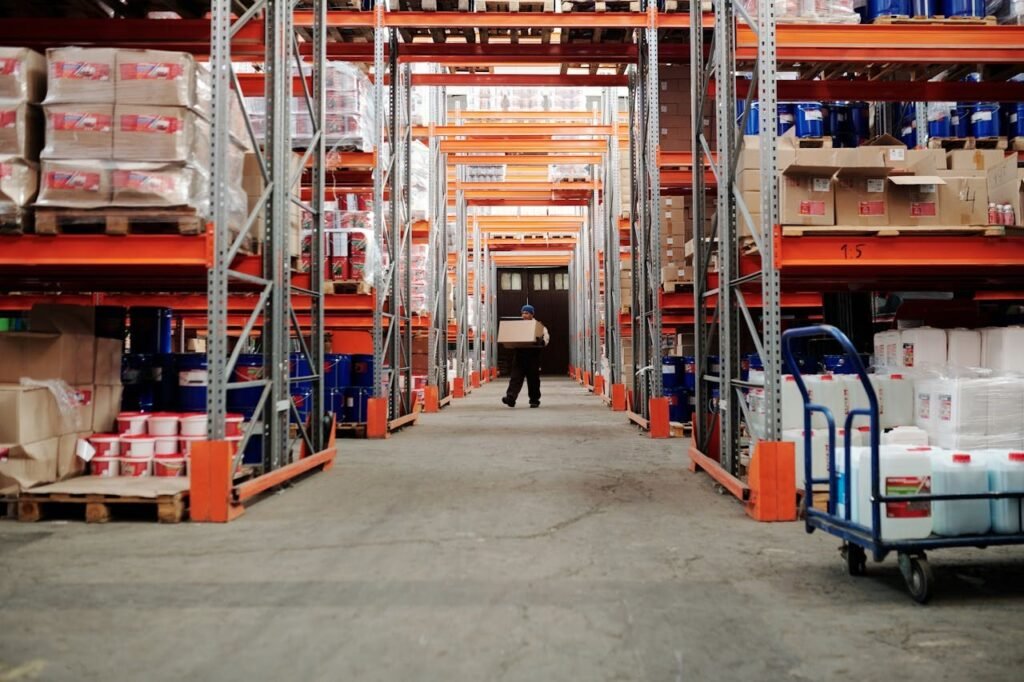
Thermal pins are much more effective at cooling than copper tubes, but engineers will have to make sure that the air gap between the pins and the mold is not filled.
Some Other Reasons for Part Deformation
Part deformation is mostly attributed to improper cooling, but some other steps of the process can also cause part deformation. Here are some common reasons you should be aware of:
- Insufficient materials inside the mold cavity
- Slow mold fill rate
- Excessive internal stress during the injection process
- Bad mold design
There is a lot that could go wrong during the injection molding process, and just one defect can cause a chain reaction that leads to your entire order being rejected by your partner. This is why you should only work with experts such as KuiXing Shanghai. With over 20 years of experience in injection molding, we are confident that we can provide the injection molds as well as the tools you need to create your very own injection molding production line. Don’t hesitate to contact us for more details.
The secrets to designing a top-tier cooling system during the injection molding process are baffles, bubbles, and thermal pins. These are design features that can help your coolants to reach hard-to-reach spots within the mold cavity, providing consistent cooling effects that will prevent part deformation as well as warpage. For more information on how our experts can help you design the perfect injection molding process, contact us right away.
Reference
https://www.linkedin.com/pulse/injection-molding-market-worth-us-43962539-million-6q5df