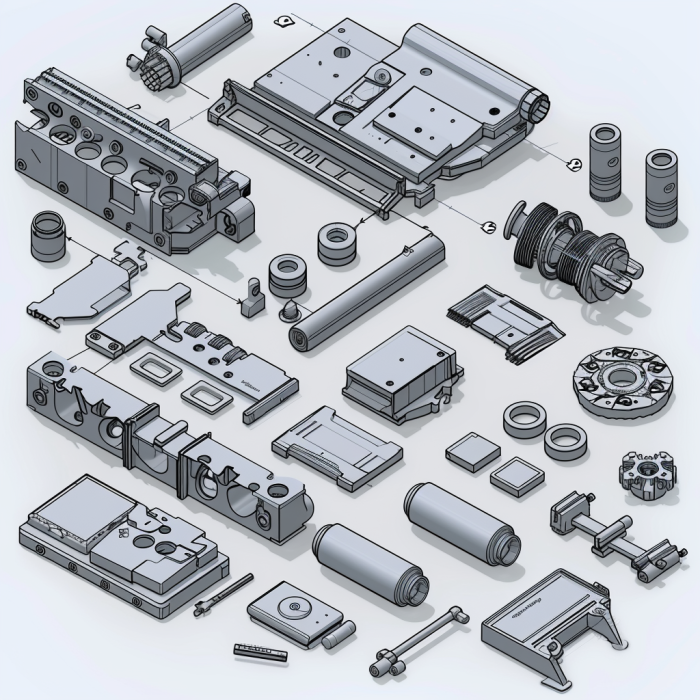
1. Accept the assignment letter
The task statement for molded plastic parts is usually proposed by the product designer, and the content is roughly as follows:
(1) Issue formal parts drawings that have been reviewed and signed.
(2) Product instructions, technical requirements, etc.
(3) Output size, delivery time, and product samples.
(4) The design brief is issued, the contract is signed, and the project will be officially launched.
2. Collect, analyze and digest original data
Collect and organize information on part design, molding technology, molding equipment, mechanical processing and special processing for use in designing injection molds.
(1) Digestion of plastic parts. Understand the use of the parts, analyze the technical requirements such as processability and dimensional accuracy of the plastic parts, such as the appearance requirements, color, application occasions and working environment of the parts; analyze the inner and outer structures of the parts, such as whether the structure has been drafted Processing, whether the design of inserts and BOSS columns is reasonable, and whether secondary processing is required after injection molding, such as electroplating, bonding, and drilling.
(2) Digestion process information. Analyze whether the requirements for molding methods, equipment models, material specifications, and injection mold structure types proposed in the process brief are appropriate and can be implemented. The most important point in analyzing process data is to understand whether the molding material can meet the strength requirements of plastic parts and whether it has good fluidity, uniformity and thermal stability.
(3) Select molding equipment. Select the size and form of equipment used for injection molding based on the existing molding equipment of the company or customer. Therefore, it is necessary to be familiar with the performance, specifications and characteristics of various molding equipment. For the injection machine, in terms of specifications, you should know the injection capacity, clamping pressure, injection pressure, injection mold installation dimensions, ejection device and size, nozzle hole diameter and nozzle spherical radius, gate bushing positioning ring size, injection mold For the maximum thickness, minimum thickness, template stroke, etc., please refer to the relevant parameters for details. It is necessary to initially estimate the overall dimensions of the injection mold and determine whether the injection mold can be installed and used on the selected injection machine. Wuxi Shangyuan New District Injection Mold Design Training
3. Injection mold ranking and mold base selection
1) Cavity layout. The number of cavities and their arrangement are determined based on the geometric structure characteristics, design requirements, dimensional accuracy, batch size, difficulty of manufacturing the injection mold and the cost of the injection mold.
2) Selection of mold base. The form of the mold base depends on the following aspects:
(1) Part geometry and overall size. If there is an undercut mechanism on the outside of the part, a lateral core-pulling mechanism of the master mold is required to demould. Considering the structure, the injection mold needs to be parted twice. At this time, a simplified thin nozzle or a thin nozzle will be considered. Mold base.
(2) Appearance requirements of parts. If the appearance of the part does not allow obvious gate marks, has high precision, and needs to be automated for production, then a thin-nozzle mold base will be considered.
(3) Mold base cost.
4. Parting surface design, pouring system form and gate location
(1) Determine the parting surface. The position of the parting surface should be conducive to injection mold processing, exhaust, demoulding and molding operations. At the same time, the surface quality of the part should also be considered to avoid the appearance of peaks.
(2) Gating system. The pouring system includes runner and gate. The gate includes its shape, location and size.
5. Analyze whether the part has an undercut mechanism, and what form of lateral parting the undercut part adopts
Determine the parting method for the undercut mechanism in the part. Generally, the slider mechanism is used for the outside undercut, and the inside undercut is generally used.
Choose oblique pin parting type. Wuxi Shangyuan New District Injection Mold Design Training
6. Determine the structural form and size of main molded parts and structural parts
Based on the structure of the part, determine which structures require independent processing of cores and inserts, and determine the size and positioning of the inserts.
Etc.
7. Determine the cooling method
Determine the cooling and heating methods, the shape and position of the heating and cooling grooves, and the installation location of the heating element.
8. Determine the ejection form, size and position of the ejection pin
Choose the ejection method, which includes five ejection methods: neck rod, ejection tube, push plate, combined ejection and cylinder.
9. Use 2D and 3D software to draw injection mold drawings and partings
1) Use AutoCAD to draw the injection mold structure drawing, which is required to be drawn in accordance with national drawing standards or in combination with factory standards and factory habits. When drawing the general assembly drawing, try to use a 1:1 ratio, starting from the cavity, and the main view and its cross-sectional view should be drawn at the same time.
The general assembly drawing of the injection mold includes the following aspects:
(1) Injection mold molding part of the structure.
(2) Parting surface and parting pick-up method.
(3) Structural form of pouring system and exhaust system.
(4) The appearance structure, connection bolts, positioning and guide positions.
(5) Mark the cavity height and overall dimensions of the injection mold.
(6) Number all parts in sequence and fill in the detailed list.
(7) Mark the technical requirements and precautions.
2) Use 3D software such as Pro/E and UG to disassemble the injection mold and draw all the male and female mold cores, cores, inserts, copper pins, sliders and bevel pins. After the design is completed, check whether the injection mold design is reasonable and whether there is interference in the injection mold parts.
10. Draw all parts drawings, proofread and review the drawings
1) Convert the injection mold parts separated by 3D software into 2D drawings, and use the 2D software to dimension the part drawings. At the same time, proofread and review all relevant drawings of injection molds. After passing the review, it will be handed over to the injection mold manufacturing department for formal processing. Wuxi Shangyuan New District Injection Mold Design Training
2) Self-examination includes the following aspects:
(1) Whether the material, hardness, dimensional accuracy and structure of the injection mold and injection mold parts meet the requirements of the plastic part drawings.
(2) Whether plastic flow, shrinkage, weld marks, cracks and draft angle affect the performance, dimensional accuracy and surface quality of plastic parts. Whether there are any deficiencies in the pattern design, whether the processing is simple, and whether the shrinkage rate of the molding material is correct.
(3) Whether the injection volume, injection pressure and clamping force are sufficient, whether there are any problems with the installation of the injection mold, the core and demoulding of plastic parts, and whether the nozzle of the injection machine is in correct contact with the gate sleeve.
(4) Whether the parting surface position and finishing accuracy meet the requirements, will overflow occur, and whether the plastic parts can be ensured to remain on the side of the injection mold with the ejection device after the mold is opened.
(5) Whether the demoulding method is correct, whether the size, position and quantity of push rods and push tubes are appropriate, whether the push plate will be stuck by the core, and whether it will scratch the molded parts.
(6) Injection mold temperature adjustment. Whether the power and quantity of the heater and the location, size and quantity of the flow lines of the cooling medium are appropriate.
(7) How to deal with undercutting of plastic parts, and whether the mechanism for removing undercuts is appropriate, such as whether the slider and push rod in the inclined guide column core-pulling mechanism interfere with each other.
(8) Whether the location and size of the pouring and exhaust system are appropriate. Whether the placement position of each injection mold part on the assembly drawing is appropriate, whether the representation is clear, and whether there are any omissions.
(9) Whether the part number, name, and production quantity on the parts drawing have been clearly marked. At the same time, it should also be indicated whether the parts are made in-house or outsourced, whether they are standard parts or non-standard parts, whether the parts processing accuracy, machining allowance, materials, heat treatment, surface treatment, and surface finishing of the injection mold parts have been clearly stated.
(10) Main parts of the injection mold, working dimensions and matching dimensions of the molded parts. Dimension numbers should be correct and do not allow the manufacturer to make conversions.
(11) Check the view positions of all parts drawings and assembly drawings, whether the projection is correct, whether the drawing method complies with the national drawing standards, and whether there are any missing dimensions.
(12) Whether the geometric structure, view drawing, dimension, etc. of all parts are conducive to processing.
(13) Main working dimensions of recalculation auxiliary tools.
11. Professional review
In principle, professional audits are conducted based on the designer’s self-proofing project, but should focus on structural principles, process performance and operational safety. When tracing, you must first digest the graphics, draw them according to the national standard requirements, and fill in all dimensions and technical requirements. After tracing, self-correct and sign. Submit the traced base map to the designer for proofreading and signature. The common practice is for the relevant technical personnel of the injection mold manufacturing unit to review, countersign, and check the manufacturing process before sending it to the public.