Contents
What is Fine Blanking in Metal Stamping
What is Metal Stamping?
What is Fine Blanking in Metal Stamping
Benefits and Downsides of Fine Blanking
Benefits
Downsides
Alternative to Metal Stamping
Plastic Injection Molding Mold
Introduce
Metal stamping is perhaps one of the oldest production methods in the history of humankind. Our ancestors have been using metal stamping since as early as the seventh century B.C. Over time, changes in stamping techniques and the Industrial Revolution have made it one of the staple production methods for many manufacturers around the world.
Fine blanking in metal stamping is a recently developed method of metal stamping that offers not just better overall performance but an amazing level of accuracy that conventional metal stamping cannot offer.
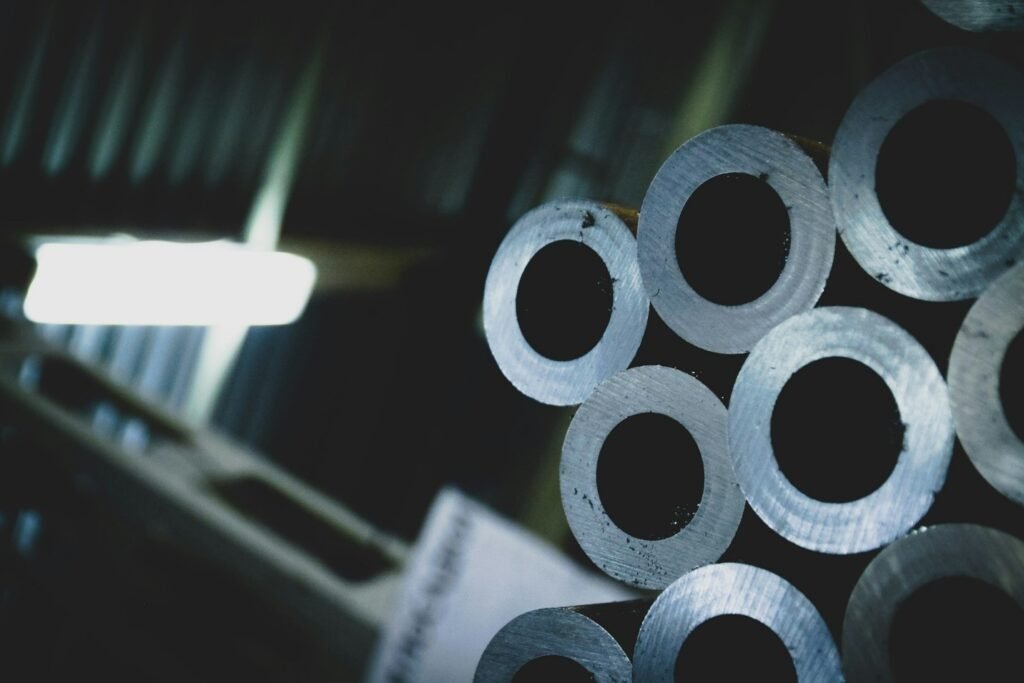
What is Metal Stamping?
Metal stamping is a production method that mainly works with malleable metals such as steel, bronze, or aluminum. This method involves tool and die surfaces that form a particular shape that you want the finished product to look like. A stamp will be positioned above these dies. When the process begins, engineers will push metal sheets or coils through the press, which will stamp them. The sheets and coils will then take on the shape of the dies and be pushed to the next stamping station until the finished product is completed.
Metal stamping is quite simple to operate, but setting up a stamping production line can be quite difficult because you need to design a streamlined process that leaves no room for error. Once the initial setup is done, you can let automation do most of the tasks with ease.
What is Fine Blanking in Metal Stamping
In conventional metal blanking, the pressure from the stamp is applied from above only, which means that there must be a clearance between the sheets and the ground. In fine blanking, there’s no need for clearance, as pressure will be applied downward and upward at the same time. This adds extra precision to the stamping process as well as greatly reduces the chance of creating tears in the process.
Conventional stamping methods don’t really care about the tearing of the metal sheet, as there’s another process called blanking to deal with it. With fine blanking, that process is combined with the stamping step to create a unified process, helping you to greatly reduce costs.
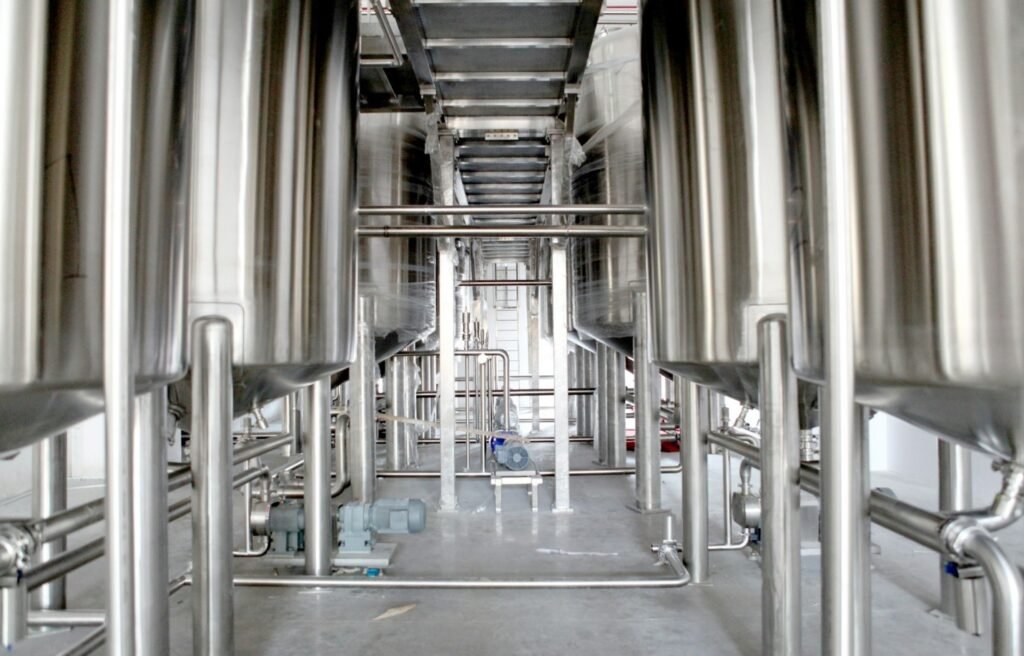
Benefits and Downsides of Fine Blanking
Benefits
The most obvious benefit of fine blanking is the immensely better level of accuracy in the end product. If you are producing airplane parts, automotive parts, and the like, then fine blanking is obviously the best choice for you, as it can take on these orders with ease.
With fine blanking, you will also not have to worry about breakage or tear and wear in the materials. Fine blanking protects the metal sheet with the counterforce from below the metal sheet, making it the more economical choice in the long run.
Then there is also the question of materials. Unlike conventional stamping, fine blanking stamping works with very durable materials such as stainless steel and superalloys, both of which are in high demand as they are materials for high-tech parts. Thus, with fine blanking, you can take on a huge variety of high-value orders.
Finally, with fine blanking, you can create complex shapes by combining the process with bending, drawing, and shearing. Conventional stamping lacks this capability, making it the sub-optimal choice for complex industries.
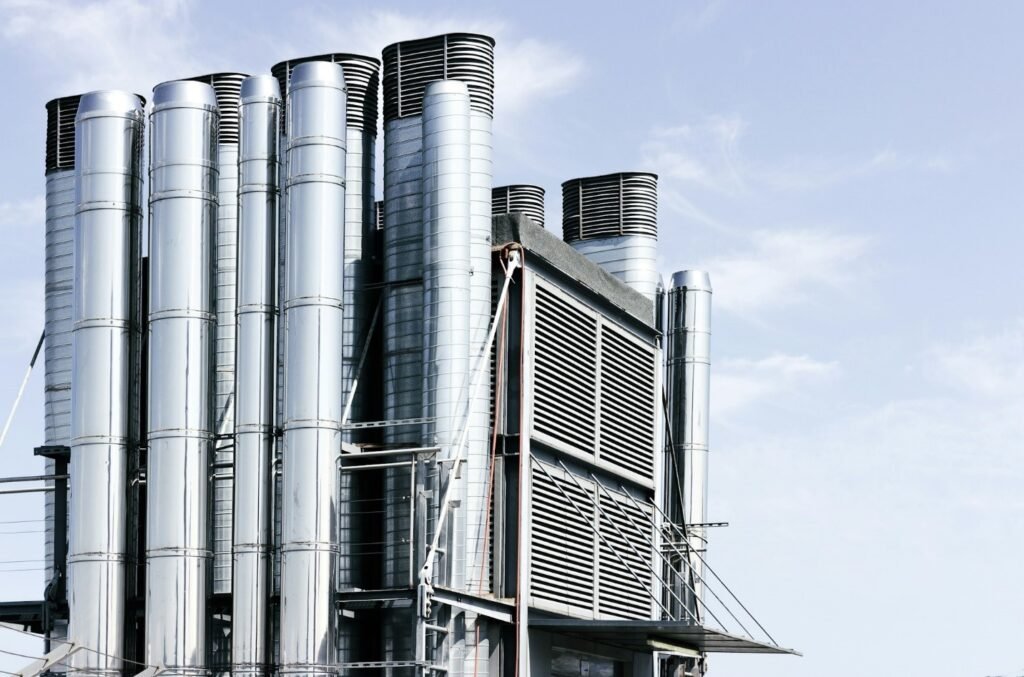
Downsides
The maintenance costs for both fine blanking tools and conventional tools are roughly the same, but you will have more tools to maintain if you choose fine blanking, so the costs might go up a little bit.
Setting up a fine-blanking production line is going to cost a lot, as you need more modern tools as well as engineers who actually know what they are doing. This will not be an easy task, especially when it comes to the engineers.
Finally, a fine blanking production line can be quite slow, due to the extra work it has to take on. However, modern technologies have greatly cut down on the production cycle of fine-blanking machines. The more advanced models can reach an impressive performance of 100 strokes per minute, making them a great investment in the long run.
Alternative to Metal Stamping
Metal stamping is a great way of producing high-quality parts, but it isn’t the only fish in the sea. Compression molding and injection molding are two great alternatives to take into account. Both of these methods can be used to produce a massive number of products, but compression molding mostly works with simple parts while injection molding can take on more intricate and complex designs. Both of these methods are also highly scalable, which enables you to easily take on high-volume orders without needing a lot of reconfiguration.
Plastic Injection Molding Mold
Injection molding is a great alternative to metal stamping, but you need to pay extra attention to one factor: The mold itself. The mold will be used to create thousands of finished products with the exact same dimensions, so one single defect in the mold means that there will be thousands of defective products down the line. Thus, you should let the experts at KuiXing Shanghai handle the mold design for you. Our engineers have had years of experience designing molds in various niches, making sure that you get nothing but the best plastic injection mold to start your project.
Conclusion
Fine blanking in metal stamping is a new process in the metal stamping field that offers better accuracy and efficiency. In this process, the metal sheets face pressure from above as well as below to maintain structural integrity and prevent breakage or tearing during the process. Fine blanking is particularly useful for producing complex parts with non-conventional designs as well as shapes, and this method can take on more materials compared to conventional metal stamping.
Reference
https://www.thomasengineering.com/blog/a-brief-history-of-metal-stamping/