Outline
- Introduction/What is injection molding plastic
- What are the benefits of injection molding plastic
- Step-by-step process of injection molding plastic
- What products are made by this process
- Conclusion
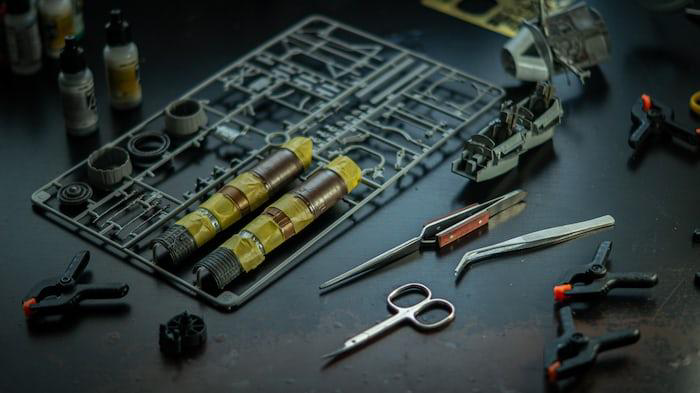
Introduction/What is Injection Molding Plastic
Have you ever wondered how this massive production of identical plastic products is done? Well, the secret lies in plastic injection molding—an unbelievable technology that uses modern machines and tools to give life to everyday items like plastic caps, phone cases, keyboards, and much more.
Plastic injection molding is a manufacturing process that works by injecting molten plastic material into a mold or cavity under high pressure to make a wide range of plastic products. This method is widely used due to its ability to create complex shapes with high precision and efficiency.
It touches our daily lives in a very subtle way: the click of a keyboard, the precision of a toothbrush, and the cap on our drink bottles. It’s in the gadgets we rely on, the tools we use, and the packaging that keeps our products fresh. This process has quietly weaved itself into our routines, and it has created efficiency and comfort in our everyday lives with useful plastic products. The amazing part is that most of these products are made in under 60 seconds!
In this article, we’ll discuss the benefits of injection molding plastic and the step-by-step process that allows the plastic to turn into the products we use every day. So let’s dive right into it.

What are the Benefits of Injection Molding Plastic?
Injection molding plastic has a lot of benefits it’s not even possible to enlist all of them in this post, so below we’ve listed some of the most important benefits of this modern technique:
Highly Efficient And Fast Production
Injection molding is one of the plastic industry’s most used and preferred processes because of its fast production. The injection plastic molding machine gives results within an hour. So, it’s a highly effective and fast method.
Flexibility In Design
Highly delicate and detailed designs can be imprinted on the plastic with precision. The secret lies in high-pressure molding which allows for better design flexibility.
Low Rates Of Scrap
This process gives off an immensely reduced scrap rate by the end of production, which is not something we see in traditional methods. Which is great for the environment!
Cost-Effective
Most of this process is handled by machines instead of manual labor. As a result, most of the budget goes to purchasing, operating, and maintenance. Moreover, since most of the products are produced in bulk, the final cost becomes even lower.
Repeatable And Consistent
Injection molding plastic is used for the production of millions of products. And these products being mostly identical results in injection molding being repeatable and consistent.
Step-by-step process of injection molding plastic
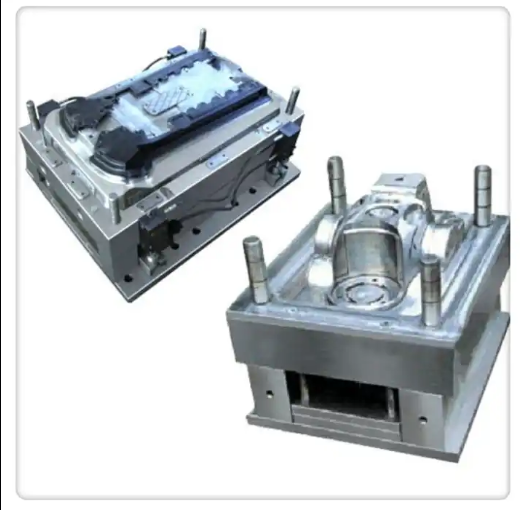
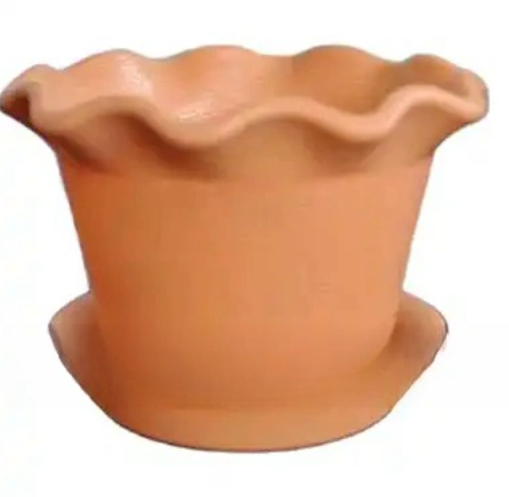
Now that we’ve established that injection molding plastic is a great technique, here’s a step-by-step breakdown of his this process works:
1. Clamping:
After making sure that the mold is clean we secure it tightly and close it. The movable and stationary halves of the mold are joined together before injecting the material.
2. Seating In:
The nozzle, mold gate, and mold runner are connected to adjust the ejector seat. This step is only necessary for trial molds or special materials.
3. Injection:
Here the injection filling phase is completed. Constant pressure is applied to pour the molten plastic into the mold.
4. Holding Pressure:
Pressure is held constant to make sure no reverse flow occurs. Holding pressure guarantees good density and mechanical strength when the material is shrunk to solidify.
5. Cooling (Melt Glue Extraction):
In step five, plastic solidifies in the mold and the cooling process begins.
6. Seat Backing:
For a seamless transition, seat buckling is done after cooling.
7. Cooling:
The process of cooling is done side by side with screw plasticization in the production stage. To get solid products without defects, the cooling time is longer than the melting time.
8. Mold Opening:
When the product is finally ready to leave the mold, the pressure in the machine is changed to get the product ready for ejection.
9. Ejecting:
The mold opens up and the ejector mechanism gets to work, smoothly pushing out the product.
10. Removing the Product:
The final product is usually removed by a robot for efficiency.
11. Ejector Reset:
Once the product is released, the machine resets itself for another round of production.
Estimating Cycle Time
The whole process is extremely fast. It takes about 6 seconds to inject the material, 10 seconds to hold it, 25 seconds to let it cool, 3 seconds to open the mold and eject the product, plus extra time for a robot or manual handling to pick up the products, adjusting the overall cycle based on the product’s design. While it might seem complex, this process allows us to manufacture products within just a few minutes.
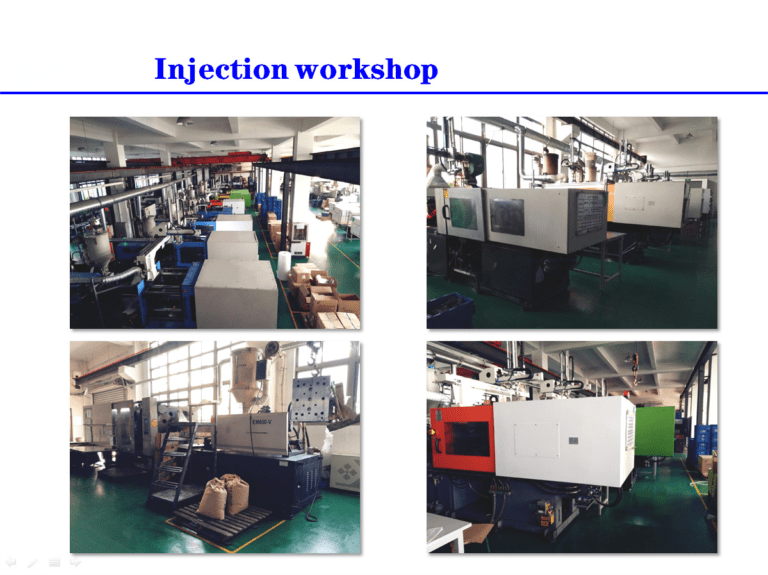
What Products are Made by This Process:
We’ve understood how this process works and what its benefits are, let me tell you something amazing. So many of our everyday products come from this method, from household necessities like kitchenware, containers, and toys to intricate components in electronics, automotive parts, and medical devices. It helps craft items that we interact with daily. It has revolutionized industries, providing a cost-effective means to produce a diverse range of high-quality plastic products that simplify and enhance our lives. You can check a wide range of useful products made from injection plastic molding machines here.
Conclusion
Plastic injection molding uses the injection method to put melted plastic in molds, which after cooling down and solidifying take the shape of the desired object. This technique helps us make durable, precise, and strong products without taking too much time or money. It is the base of the plastic processing industry, in fact, it is the technique that makes it possible for companies to make thousands of complicated and unique products in a matter of minutes! We can say that it isn’t just an industrial process; rather, it is the wizard behind a lot of magical little things that make our lives easier every day.
External links: